LASER - World of PHOTONICS 2023: Laser Material Processing
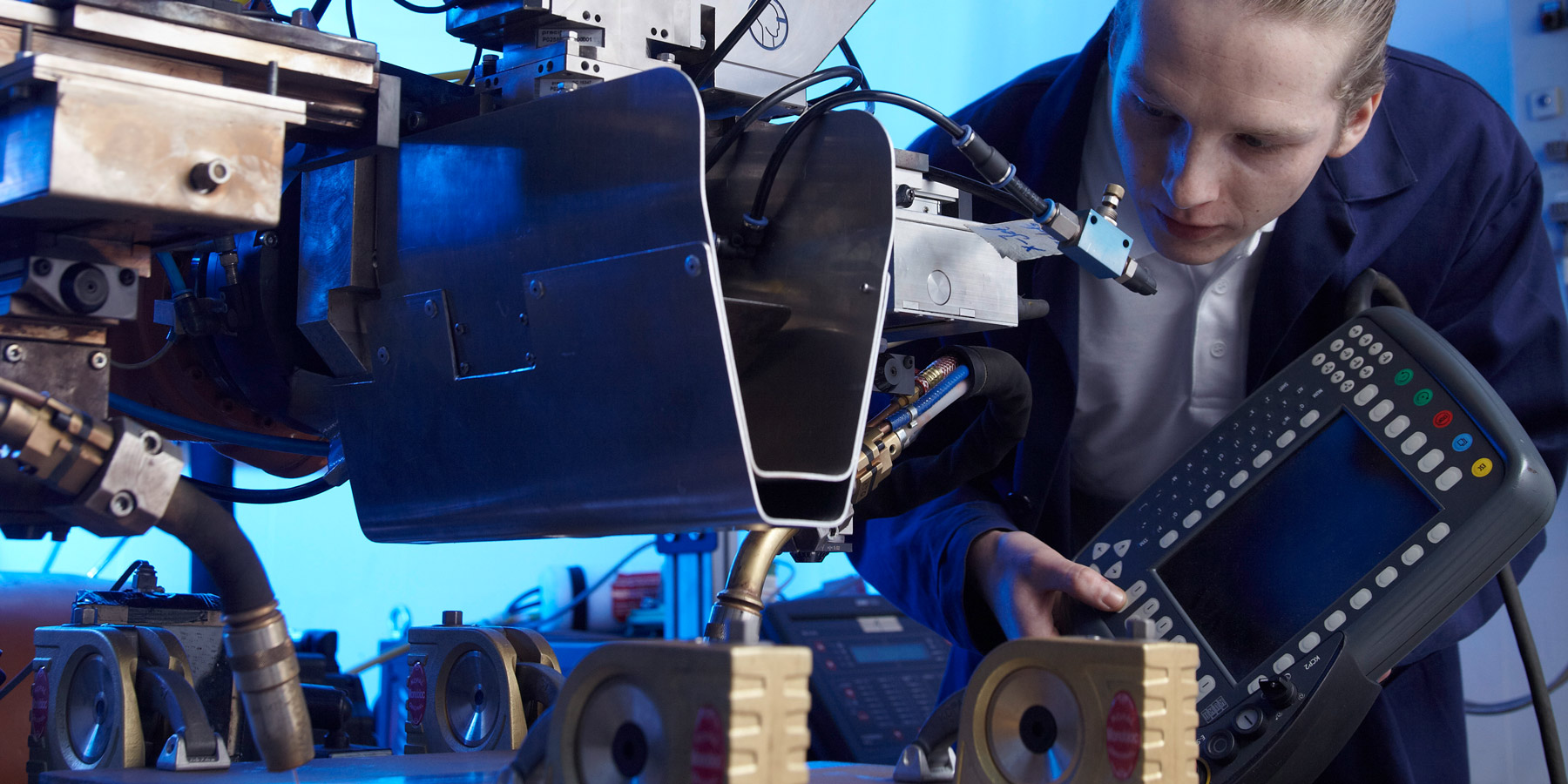
Contact
Phone: +49 511 2788-419
Email: messe@lzh.de
Steel and aluminum
Laser beam welding of thick dissimilar steel and aluminum joints
Motivation
• Lightweight construction in shipbuilding to reduce CO2 emissions and increase ship stability
• Joining of steel with aluminum by explosion welding (complex, time-consuming, and cost-intensive joining process)
• Low strength → oversizing and low design freedom of explosion-welded joints
Function / Properties / Characteristics
• High potential for efficient laser beam welding of form-fit dissimilar joints of steel and
aluminum with high strength → no oversizing → higher design freedom
• Generation of an undercut by two-sided, crossing laser beams
Applications
• Shipbuilding (Connection of steel hull and aluminum superstructure by means of adapters)
• Wagon construction
• Scaffolding construction etc.
Parameters
• Laser power: ≈ 6 kW
• Welding speed: ≈ 1,0 m/min
• Angle: ≈ 15 – 30°
Laser sources
• HighLight FL6000-ARM (COHERENT, INC.)
• Fiber Laser
• ARM: Adjustable Ring Mode
Processed material
• Steel S355 (t = 5 mm)
• Aluminum alloy AA 6082 (t = 10 mm)
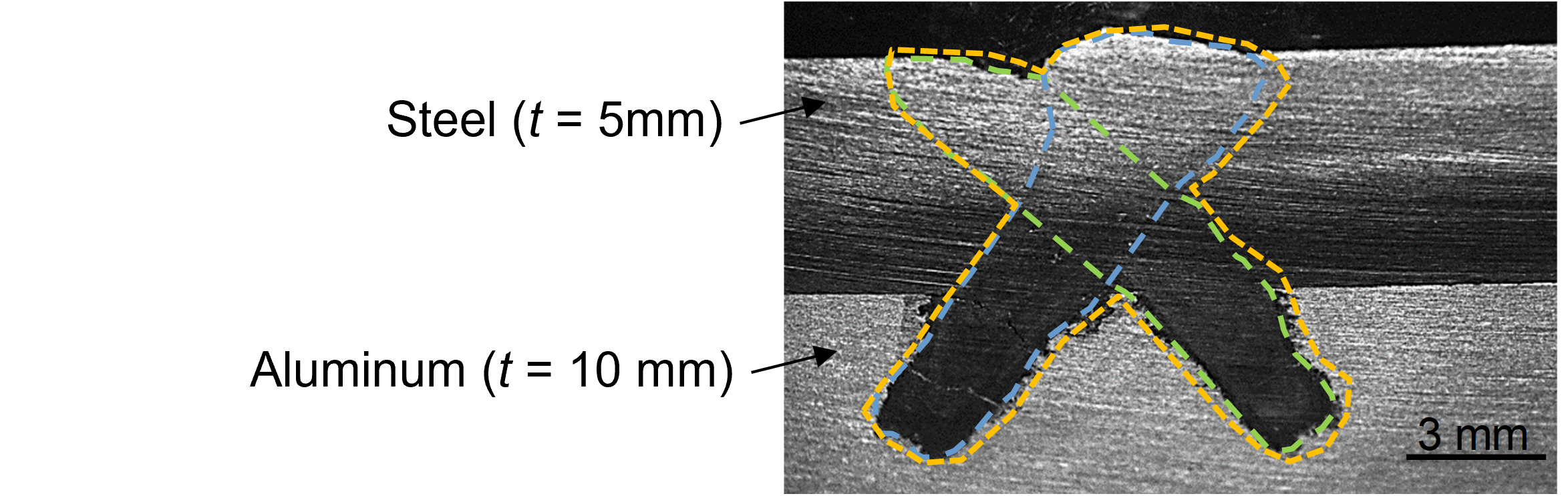
High-power diode laser beam welding of thick steel plates
Motivation
• Decrease of production time and costs
• Increase of economic efficiency, conserving resources (energy, gas, wire)
• Substitute multi-layer arc-welding (very time-consuming) and hybrid welding (limitation in terms of thickness)
Properties / Characteristics
• Very high penetration depths
• Single-layer -> very fast
• One-sided
• Butt joints up to 22 mm crack-free under laboratory conditions
Applications
• Shipbuilding (butt joint, T-joint)
• Offshore structures
• Pipeline manufacturing
• Bridge construction
• Structural steelwork
Parameters
• Laser beam power = 40 – 60 kW
• Welding speed = 0.5 – 1.5 m/min
• Focal diameter = 4 mm
• Wire feed rate = 5 – 20 m/min (for butt joint)
• Ceramic weld pool backing (for butt joint)
Laser source
• LDF 60,000-200 (Laserline GmbH)
Processed material
• Steel A36 (t = 15 – 30 mm, with face milled abutting edges)
• Solid wire electrode (G4Si1, Ø = 1.2 mm)
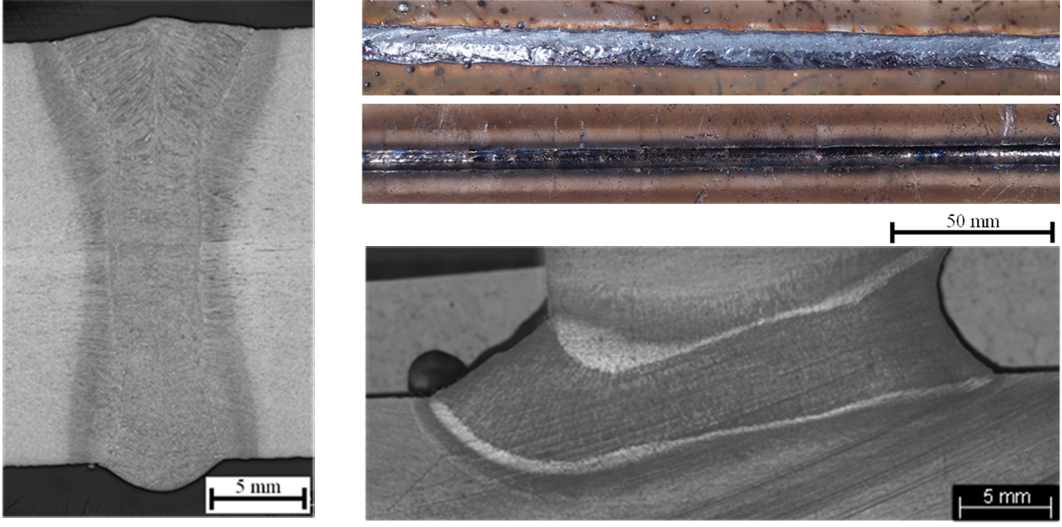
Silica glass
Laser welded fused silica
Motivation
• Fiber-based laser welding process for fused silica as a replacement for conventional gas flame processing
• Automated process for reproducible parts and better working conditions
Properties
• Transparent and homogeneous weld seam
• Material bonding/connection of the glass with no defects
Parameters
• 3 mm thick fused silica substrates and 400 µm thick fiber
• Process speed: up to 1 mm/s
• Angle of the glass plates: 90°
• Output power: 160 – 170 W
Applications
• Production of fused silica components for the semiconductor industry
• Chemical and medical equipment manufacturing
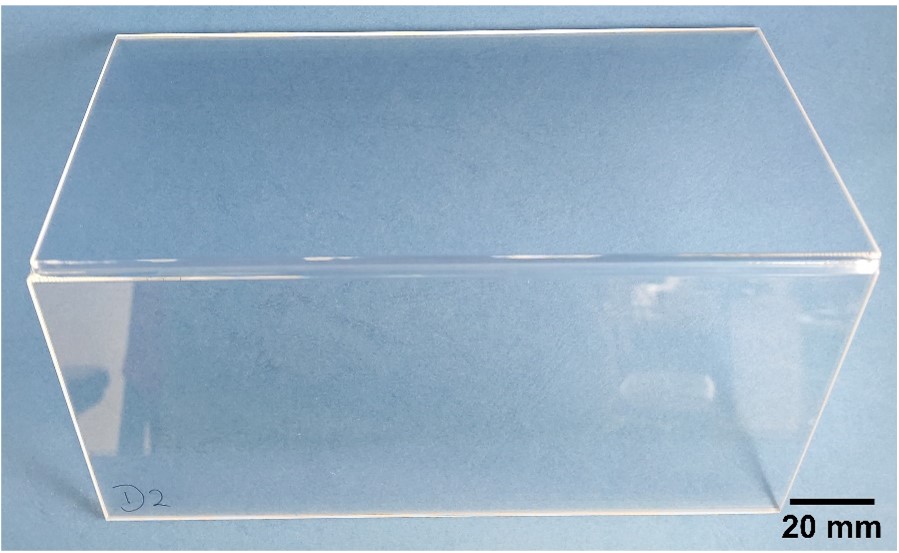
Colored skyline of Hannover on fused silica glass
By coloring glass, it is possible to apply different layouts and designs. The color is applied by means of an airbrush system. The consistency of the color and the spray pressure influence the coating result. The desired layout is generated via software.
A CO2-Laser with a galvanometric scanner is used. This enables the deflection of the laser beam and generates the colored motif by selecting the appropriate parameters such as working distance, laser power, scanning speed, and hatch. After the laser processing, the excess color is wiped off with water and a wipe.
Motivation
• Colored design of flat glass
Function/Properties/Characteristics
• Local laser burning of the color on glass
• Color is burned into the glass and bonded
• Thickness of the fused silica glass: 3 mm
• Thickness of the coating: 30 µm
• Good contrast
Applications
• Coloring of flat glass, e.g. architectural glass
• Colors like blue, black, and green are possible
• Colored designs on different glasses are possible
• Glasses like soda-lime-glass, borosilicate glass, fused silica glass
Parameters
• Special blue color for laser processing
• Layout: skyline of Hannover
• Coating of the color: ca. 30 µm
• Scanning speed: 1500 mm/s
• DC = 28 % (DC=Duty Cycle)
Laser sources
• CO2-Laser (Diamond Cx -10, Coherent)
Processed material
• Fused silica glass with a thickness of 3 mm
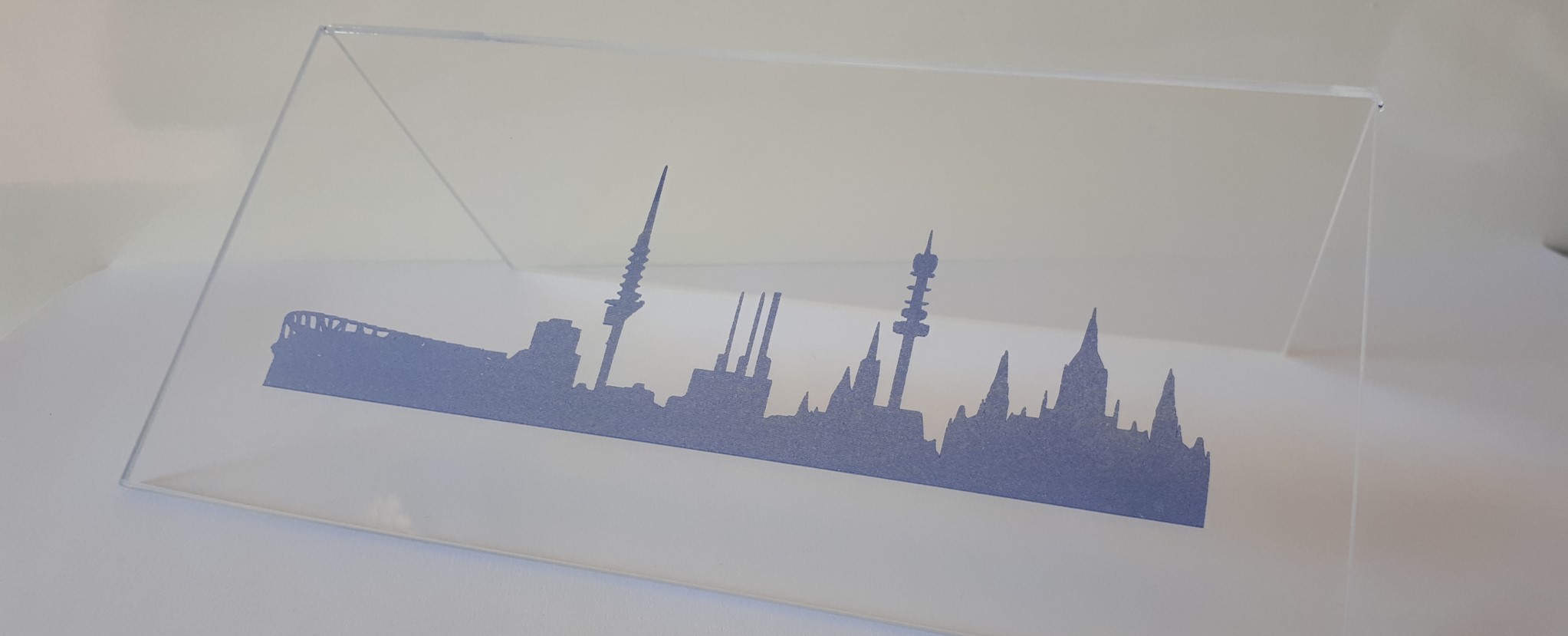
Welding of NFRP
Motivation
• Development of a welding process for natural fiber-reinforced composites
• Local functionalization of components with thermoset matrix for weldability
• Fulfill olfactory criteria of components for airplane interior
Function / Properties / Characteristics
• Integrating thermoplastic layers in the NFRP production process
• Simultaneous welding with a large-area surface emitter
Applications
• Laser transmission welding of thermoplastics and fiber-reinforced thermoplastics with natural, carbon, or glass fibers
• Welding of components without thermal damage to the natural fibers
• Fast welding of complex-shaped geometries
Laser sources
• VCSEL array-based heat source
• Wavelength 980nm
• Max. power up to 2.4 kW
• 12 independent emission zones
Processed material
• Hemp, flax, and wood-based natural fiber-reinforced plastics with epoxide and phenolic resin
• Thermoplastic layers based on polypropylene, polyamide, and polyetherimide
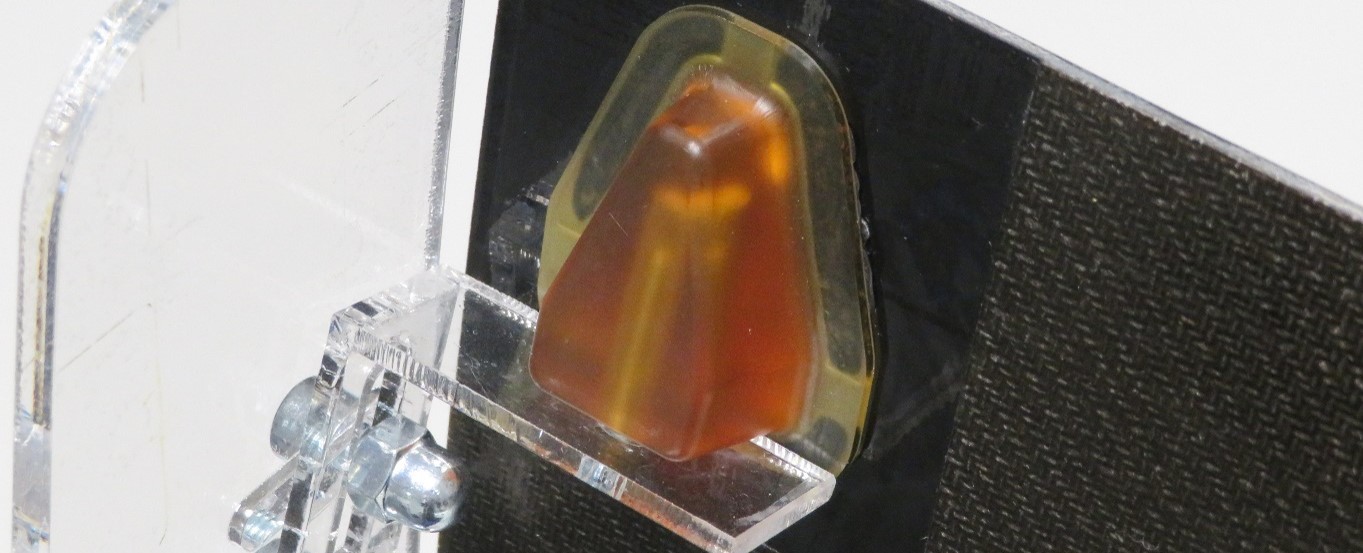
Drilling of CFRP
Motivation
• >150 000 000 drilling operations performed per year in the German aviation industry
• High tool wear when machining CFRP with drill bits
• High quality and high accuracy required
Function / Properties / Characteristics
• No tool wear with laser drilling
• Flexibility in bore diameter and drilling pattern without tool change
• Multi-material stacks drillable, incl. sandwich materials
• High quality and high accuracy:
• Heat affected zone <40 µm, drilling without taper
Applications
• Macro drilling:
• High-quality rivet hole drilling
• Micro drilling of large surfaces:
• Noise reduction & sound design in aerospace/automobile/construction industry
• Flow control/boundary layer suction
Parameters
• Remote processing
• Stepwise material ablation
• Parallelized processing with beam splitting
Laser sources
• Nanosecond-pulsed high-power laser by TRUMPF
Processed material
• Carbon fiber reinforced plastics, Glass fiber reinforced plastics, CFRP-Sandwich materials
• Multi-material stacks drillable (e.g. thermoset CFRP laminate with thermoplastic laminate
including GFRP protection layer and copper mesh)
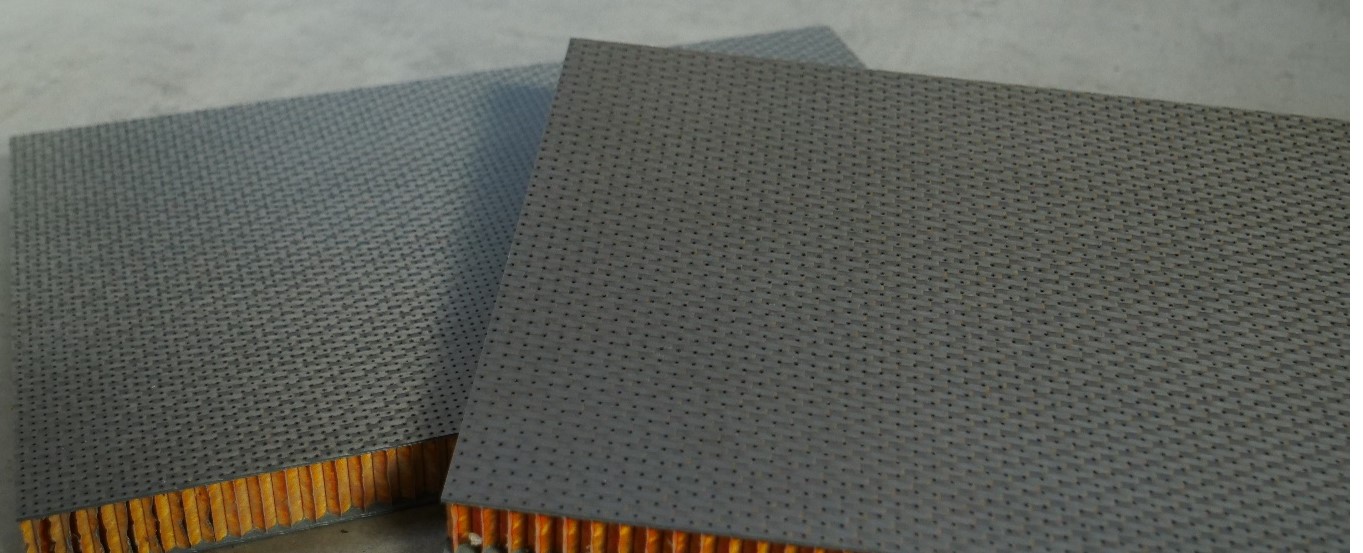