Smart production
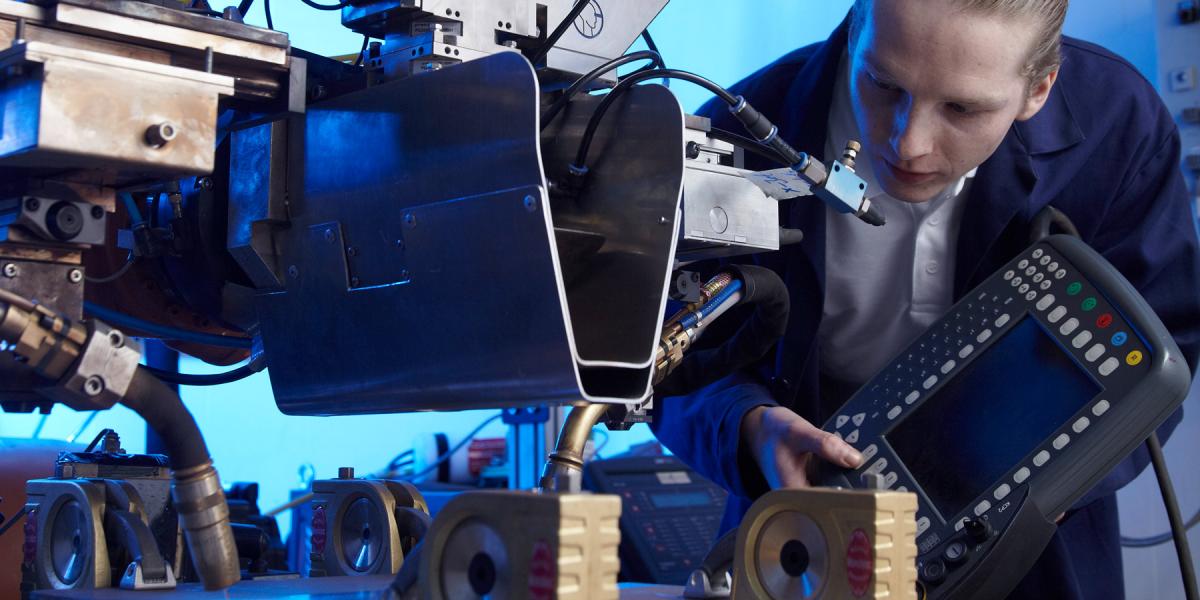
The production of the future is digital, connected, and enables real-time process monitoring. Our smart production with the laser is also energy-efficient and resource-saving. Laser material processing allows innovative manufacturing methods and connected processes. Our processes can be used for various materials from the nanometer to the large-scale range, including semiconductors and other materials.
Your contact person
Dr.-Ing. Peter Jäschke
Laser processing of metal
Compared to conventional methods, processes with lasers can be more energy- and time-saving or enable entirely new approaches. We develop novel processes for metal processing and combine them with monitoring and control methods. We are also developing many processes for underwater use.
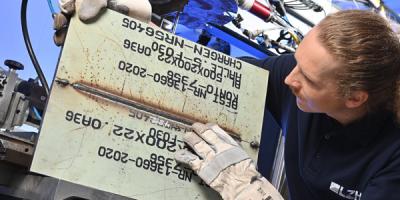
We work on innovative, automatically controlled processes for laser beam welding – from thin to thick sheet metal. Our ideas start where conventional methods reach their limits. For example, we develop welding processes for sheet thicknesses > 30 mm with laser powers > 40 kW, or micro-welding processes for e-mobility. We achieve high process reliabilities and seam qualities through the intelligent combination of processes and materials. The research of laser beam soldering processes is another focus for us. We develop micro-soldering processes for very small components down to the 50 µm range or soldering processes in an oxygen-free environment for aluminum alloys. For our processes, we work with continuous and pulsed lasers depending on the requirements.
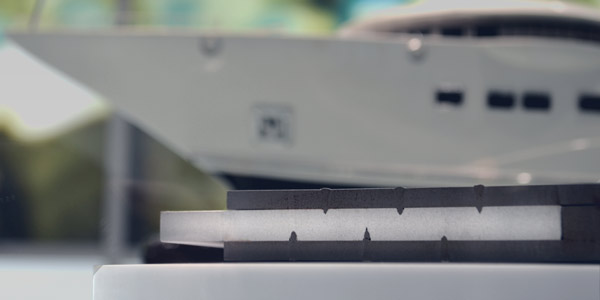
Mixed joints each have their own challenges, especially in dissimilar joining. Challenges for mixed joints are the formation of intermetallic phases, low metallurgical solubility or the different absorption properties of the joining partners. With artificial intelligence and the statistical design of experiments, we can meet these challenges individually. Dependencies on target variables are identified, process parameters optimized, and process windows extended. For production, we work on safe and stable joining of:
- Steel to aluminum
- Aluminum to copper
- Copper to steel
- Glass to metal
- Kovar to sapphire
- Invar to quartz
- Metal to plastic
- Metal to textile
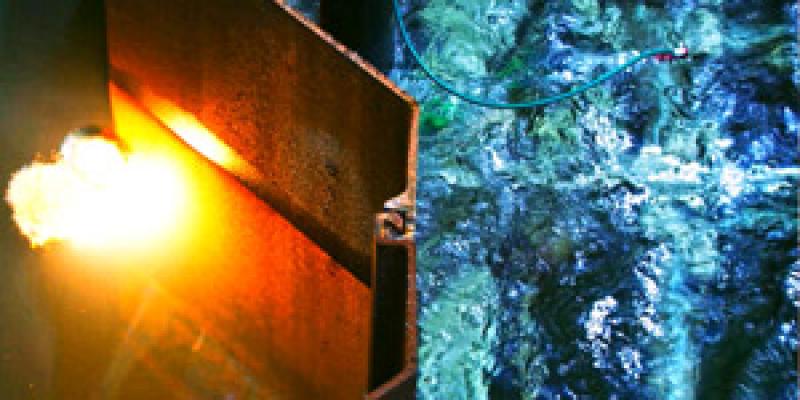
Lasers work automatically, without contact, and do not expose the material to mechanical stress. Laser cutting is established in many industries, and we see development potential here, for example, through smart monitoring and control. In this way, the energy input can be precisely controlled and regulated in an automated manner. We work on the intelligent cutting of films or developing automated, controlled processes for clean-cut edges and precisely specified geometries. To cut widths and accuracies down to the lower micrometer range, we use ultrashort pulse lasers and develop process strategies that enable minimal heat input into the workpiece despite optimizing process time. For underwater cutting, the reliable separation of components is of great importance. For this purpose, we develop processes with high productivity and laser safety.
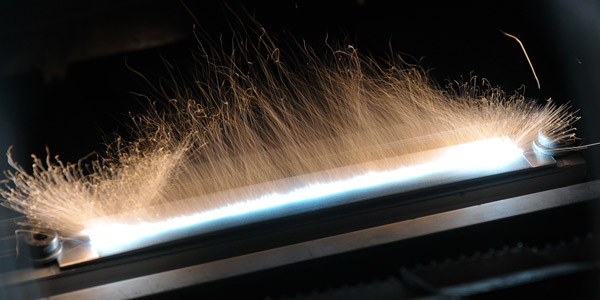
Hardening, alloying, dispersing, structuring, and functionalizing - we automate and optimize the processing options on the component surface with our laser machining processes. Joint preparation and the roughening of internal structures are further interesting focal points in the field. Our goal is to achieve processes with high speeds and outstanding surface qualities. We functionalize metal surfaces by changing the micro- to nanometer range surface topography with ultrashort pulse lasers. This makes it possible, for example, to produce more efficient electrodes for electrolysis, from which the resulting gas bubbles roll off more easily.
Laser processing of polymer and composite
When processing plastics and composites, the laser plays out its many advantages: it operates without contact, has minimal wear, the heat input can be regulated very precisely, and the processes can be automated.
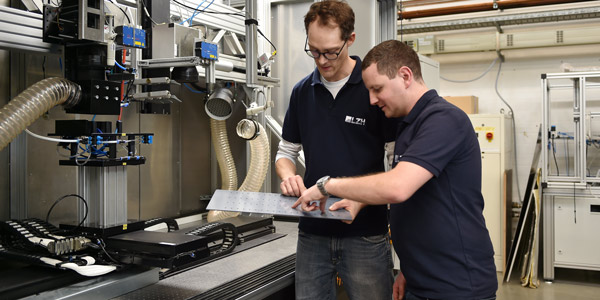
We develop processes for laser joining of plastics and composites. In doing so, our processes enable the stable connection of large-area fiber composite structures as well as delicate and precise weld seams of electronic components. We combine laser-based processes with different monitoring methods to implement process monitoring and control. This enables us to join even composite structures safely and stably with consistent heat input. We work on heat conduction and laser transmission welding processes and enable automated processes for lightweight manufacturing.
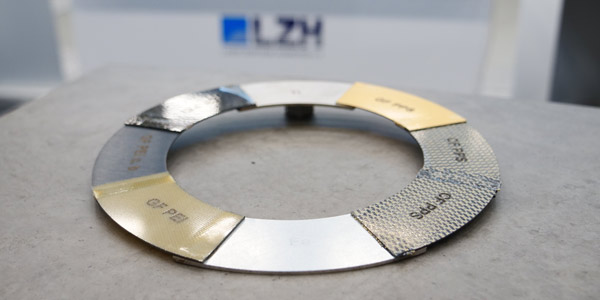
We work on both similar and dissimilar mixed joints, such as metal to plastic. We weld different, chemically compatible plastics together or join plastics to metals with laser beam welding or laser transmission welding. We achieve high-strength joints and replace costly adhesive bonding processes with the right measurement and control technology.
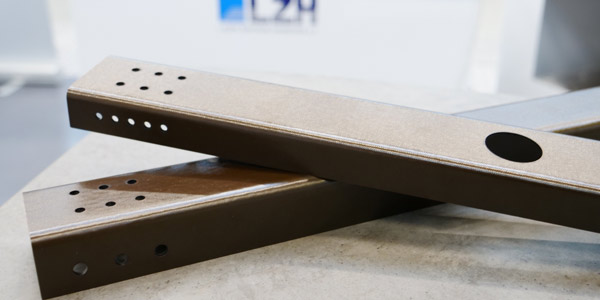
We work on very fast and highly automated processes in laser-based drilling and cutting of carbon fiber reinforced plastic (CFRP) and sandwich structures. This allows us to set varying hole sizes and geometries even in different materials in the shortest possible time. This saves tool changes and thus setup time. Furthermore, we develop trimming processes for CFRP, which are characterized by their wear-free nature. With our trimming processes, we achieve very precise energy input and maintain manufacturing tolerances for high-performance applications. In addition, we develop cutting processes for very thin films and deal with novel materials and material combinations.
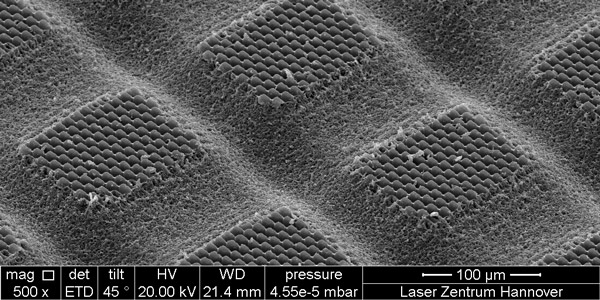
In the field of surface processing, we deal with structuring, alloying, dispersing, functionalizing, ablating, and cleaning surfaces in the centimeter to the nanometer range. With automated laser ablation, we prepare fiber composites and other materials for repair. We can change the topography and chemistry of plastic surfaces to produce special properties. Application fields are decor, plagiarism protection, tribology, haptics, liquid wettability, and cell adhesion. Without chemical changes, plastic components with functional surfaces can be produced very cost-effectively in large quantities by injection molding using laser-structured injection molds.
Laser processing of glass and ceramic
The material glass has challenging material properties, which means that many processes for manufacturing components are still carried out by hand. The laser is a standard tool for post-processing glass components. Glass processing becomes automatable and reproducible through process control and regulation. We work on innovative processes for ceramics as well.
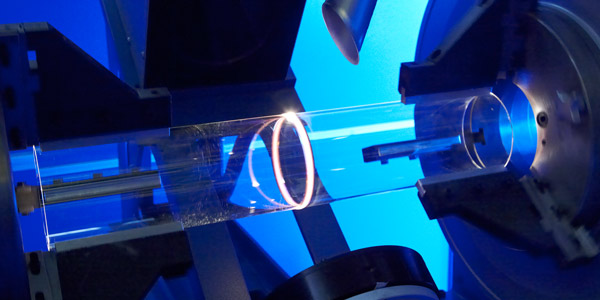
With the laser beam welding of glass with filler materials such as powder or glass fibers, we join several millimeters thick glass and bridge material gaps. This is particularly interesting for architecture and chemical apparatus engineering but can also be used for other applications. By monitoring the process using a pyrometer, we want to enable very precise temperature application so that the material's structure is not damaged. Via a downstream annealing and polishing process, we achieve high seam qualities without stresses in the material.
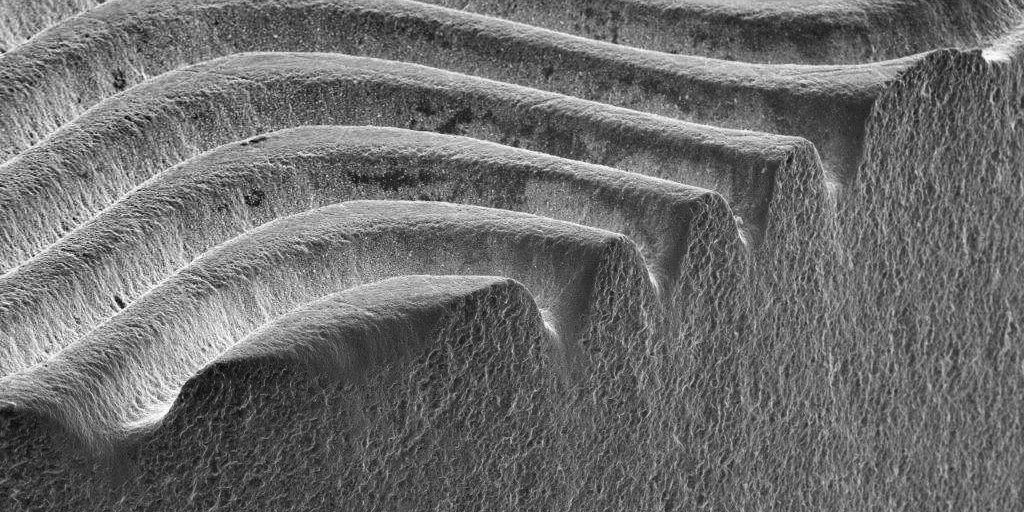
We process glass and ceramic surfaces three-dimensionally with the laser. In this way, we create, for example, lenses for focusing sound or anti-reflective surfaces for microwave applications. As a transparent material, glass can also be processed in volume. Here we use ultrashort pulse lasers to create defined submicrometer defects, for example, used as a standing center reference for particle or scattering measurement systems.
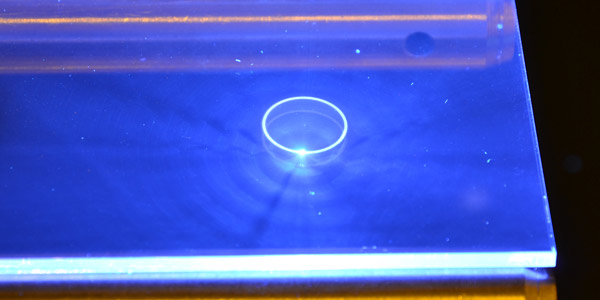
Drilling and cutting glass and ceramics with high-quality cutting edges is very feasible with lasers. We work on precisely monitoring and regulating the energy input during the cutting process so that even ultra-thin glass with thicknesses < 100 µm, for example for the semiconductor industry or display technology, can easily be cut. But cutting thicker substrates and complex contours also requires precise monitoring and control of the process for successful implementation.
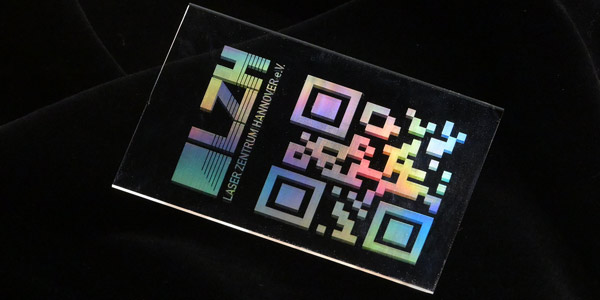
To mark medicines or other products in a forgery-proof way, we develop special security markings on glass, such as diffraction structures. These are also suitable for clearly tracing product chains. We are also working on using lasers to introduce long-lasting colored markings into the glass surface, applying optical functional layers to glass, and allowing ions to diffuse into the glass volume.
Plant and system technology
In addition to process development, we also design and manufacture the required plant and system technology. Our processing heads are tailor-made for specific applications or enable uses not previously commercially available. We integrate components and controls into complete systems. In doing so, we place a particular focus on work and laser safety and the ability to incorporate them into automatic process sequences.
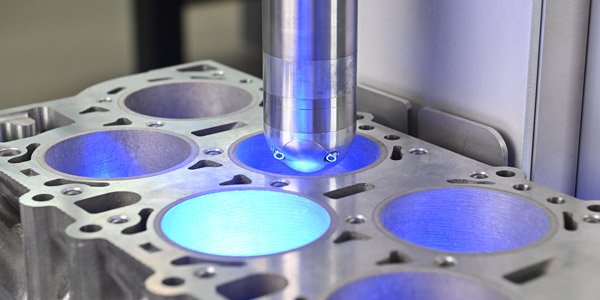
Direction-independent, split beam or special operating conditions - we develop laser processing heads adapted explicitly to specific applications and processes. We design and manufacture the necessary hardware and software and integrate them into existing plant technology. In doing so, we focus on a close integration of process and process technology as well as sensor technology and easy handling of the technology. We develop innovative approaches that make their way into production, for example for coaxial buildup welding or the processing of internal structures.
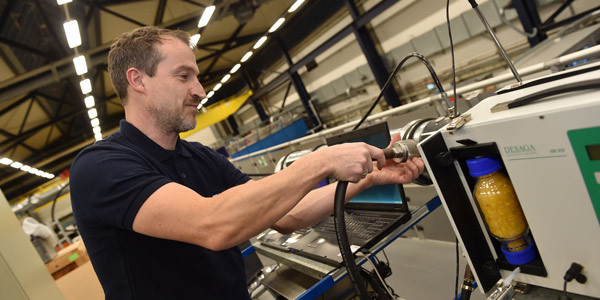
For safe working with lasers, we work on the necessary safety technology and research measurement methods for novel processes and materials. For this purpose, we work on emission characterizations and predictions for materials such as metals, polymers, and composites. We also perform irradiation experiments. The assessment and characterization of primary and secondary radiation is another focus of our research. Our research also includes the carry-over of the smallest particles in the nanometer range, e.g. in composite material processing, from work into homes. With our findings, we co-develop safety standards.
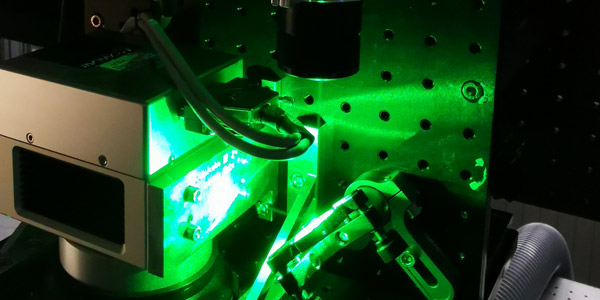
In the field of special mechanical engineering, we advise and support the development of plant technology. We develop, manufacture, and deliver single components up to complete plants. In addition to the hardware of mechanical components and control technology, we develop the necessary software and programs. Plant and operator safety are essential to us. For example, for the research of processes under the exclusion of oxygen atmosphere, we develop equipment and system technology for soldering and additive manufacturing in a powder bed with silane gas protective atmosphere.
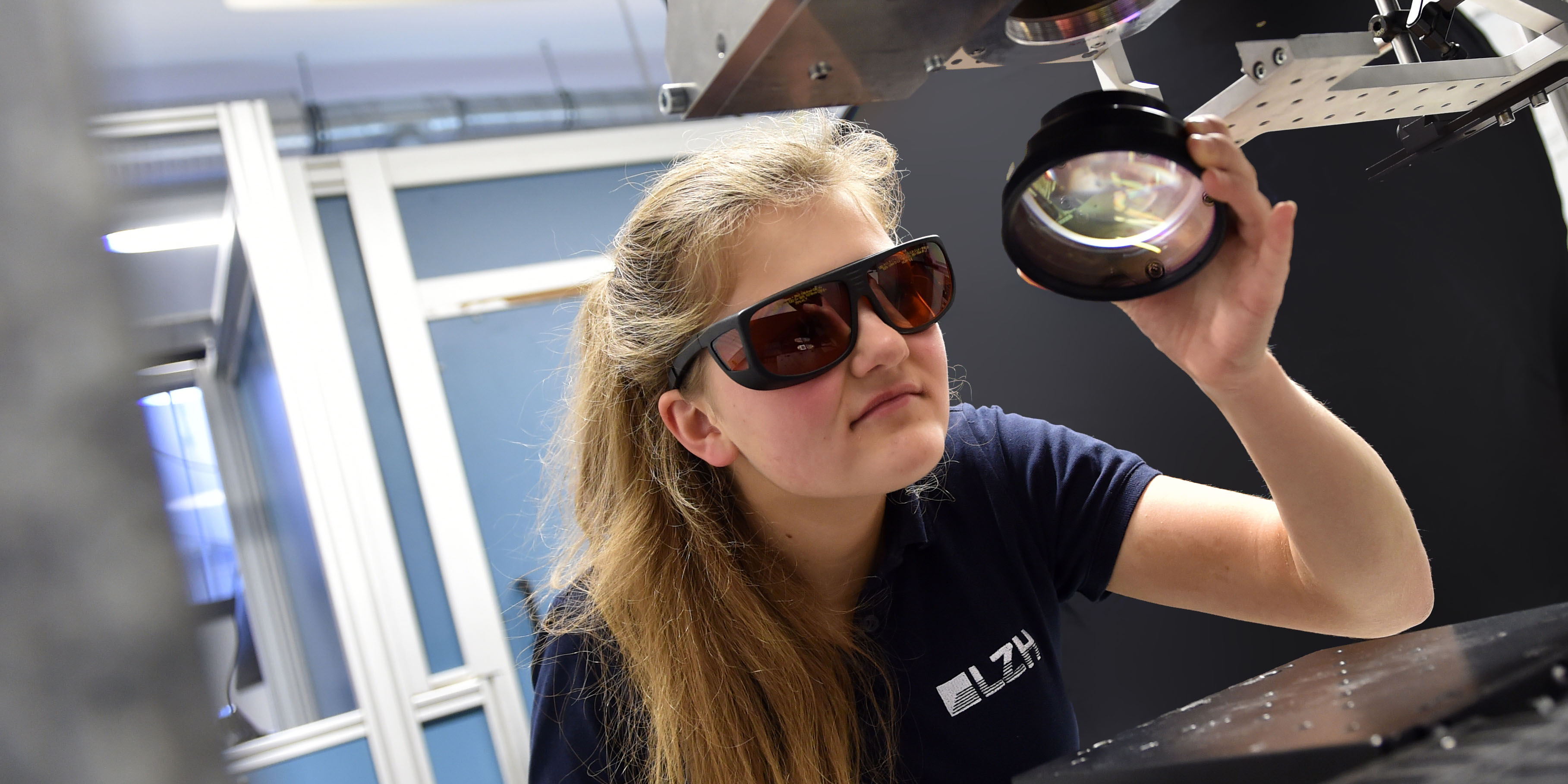
Faster or more efficient processes can be achieved through parallelization. On the one hand, we are working on using several lasers side by side to increase production speed or improve the process itself. On the other, we are developing hardware that can map multiple individual spots. In addition to these energy-distributing process parallelization techniques, we are also working on pulse-distributing process parallelization techniques. These work - locally - with reduced pulse repetition rates. This allows the high pulse repetition rates of current ultrashort pulse lasers to be fully exploited without excessive heat accumulation.
Process monitoring and quality assurance
The goal of our work in the area of process monitoring, control, and regulation is a production that functions at maximum speed without loss of component quality. We want this to work even for individual single-part production. Additionally it should minimize the costs of process development. To achieve this, we connect processes with monitoring methods, develop self-learning process control algorithms, and integrate them into existing processing systems. We additionally ensure the quality of the components through classical analyses.
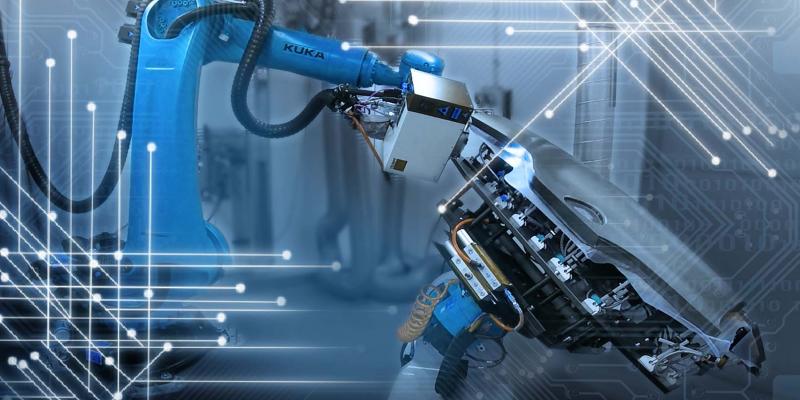
In the future, we want to use self-learning systems to link process monitoring and control to an online control system that actively and automatically intervenes in processes and adapts them to changing conditions. We are working with partners to teach algorithms basic principles and use artificial intelligence to read and evaluate data and feed it back into the process. With hyperspectral cameras, we can already determine surface roughness during the process using artificial intelligence.
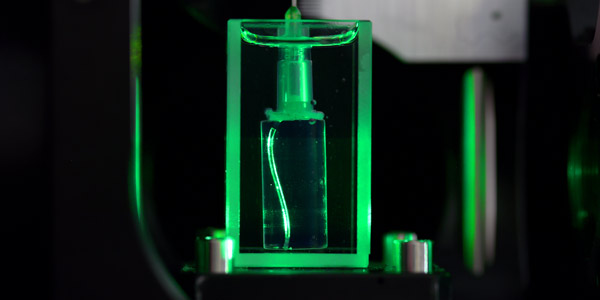
We thoroughly analye semi-finished products and finished components for pore formation, layer thickness, and their suitability through hardness tests, among other things. We develop non-destructive analyses using optical coherence tomography (OCT) and emission analyses. To draw conclusions about the quality of automated processes and continuously improve them, our scientists also use:
- scanning electron microscopy (SEM)
- nano-computed tomography (Nano-CT)
- energy dispersive X-ray spectroscopy (EDX)
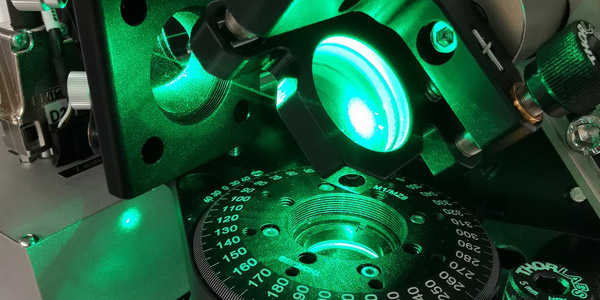
Ever faster processes require equally fast, smart control and regulation technology. Our goal is to record relevant process variables in processes with pulsed laser systems with pulse accuracy. This would make it possible to determine new process variables between the laser pulses and control the process actuators appropriately. The interaction of fast, pulse-to-pulse real-time capable sensors, data processing, and actuators is the basis for this. We develop suitable software and the necessary analog and digital electronics for signal processing and actuator control. We want to generate further input variables for process control via process models and implement self-learning control strategies in such systems.
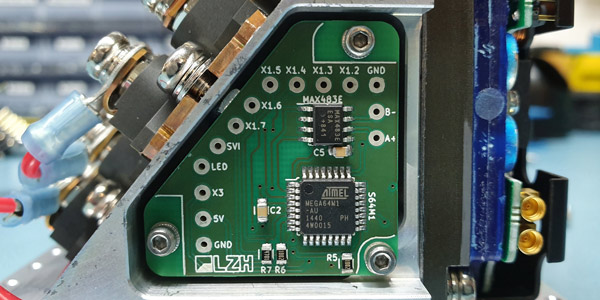
We improve and combine process sensor technology for laser material processing to manufacture high-quality components. In interaction with artificial intelligence for data evaluation and Convolutional Neural Networks (CNN), we thus aim to enable real-time analyses and, in particular, online monitoring and thus high process reliability. We work with:
- photodiodes
- pyrometry
- thermography
- high-speed cameras
- hyperspectral camera (process emissions)
- optical coherence tomography for distance measurement during ablation and for welding depth measurement
- camera based measurement methods
- optical microphone