Smart space technologies
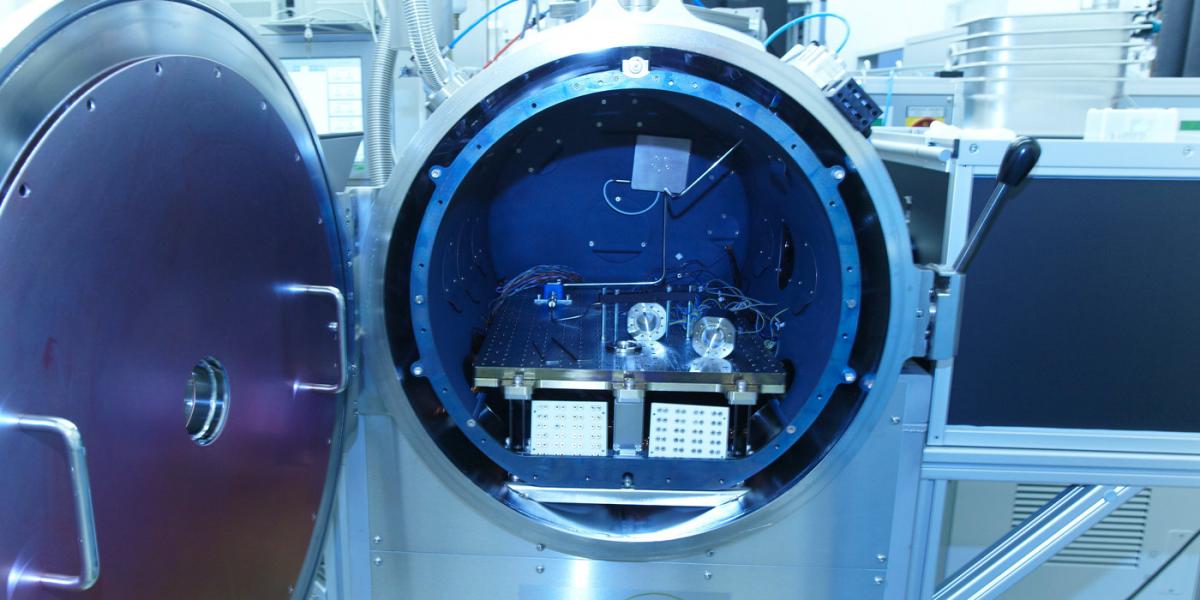
For decades, we have been developing and manufacturing robust, space-qualified laser systems, fiber components, and dielectric coatings for optics that are specifically designed for the application in question. We enable new innovative applications with our smart space technologies, from the search for life to production in space and on planets. We supply our flight hardware to ESA and NASA, among others.
Your contact person
Dr. rer. nat. Jörg Neumann
Overview of smart space technologies
Space-ready designs
Technologies for space must withstand the most adverse conditions, such as high temperature fluctuations and ionizing radiation. We are specialists in designing and constructing space-qualified optical systems for long-term use in space - for sustainably successful space missions. We are continuously expanding our expertise and testing capabilities and enabling new innovations with intelligent approaches.
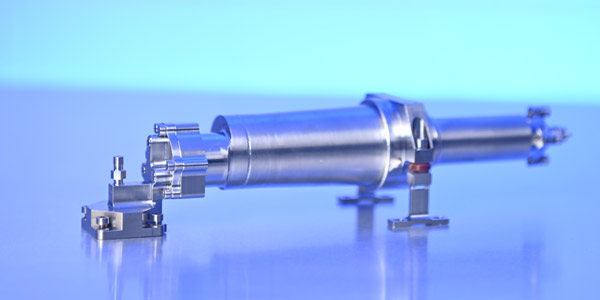
Sensitive lasers must reliably survive launch, flight, and landing and withstand the changing conditions on planets, satellites, or directly in space. We adapt the laser design to the specific conditions by optimizing the design optically, mechanically, and thermally. Since lasers are often very alignment sensitive, we create mechanical designs that reliably ensure laser alignment over a wide temperature range, enabling smart reliable lasers for very specific applications.
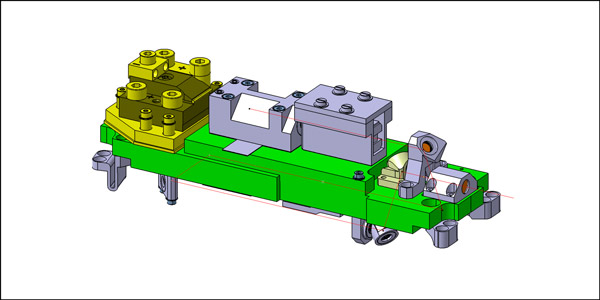
We run simulations to test laser designs for their opto-mechanical properties. In this way, we ensure that the designs are suitable for use in space and fulfill their functions before the hardware is created. Optical simulations such as ray tracing or wave propagation are combined with structural and thermal simulations (finite element method). We are constantly developing our methods further.
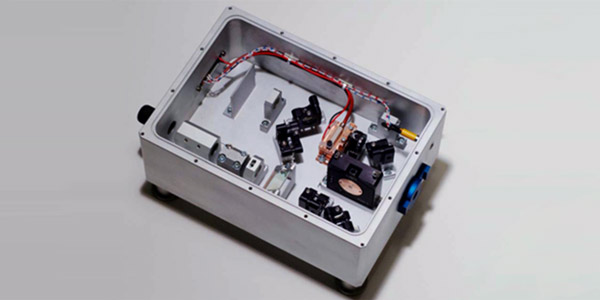
There can be several hurdles between the idea and its implementation. In feasibility studies, we examine in advance what can be implemented in space and how and what challenges have to be taken into account on the way into space. We derive the necessary budgets for mass and energy and estimate the development and implementation costs. We cover the entire development process, from paper studies to prototypes and flight hardware. For this, we use our many years of expertise and the latest knowledge from laser and component research.
Laser systems
Laser systems for space must be small, compact, and at the same time very robust. They must withstand strong temperature fluctuations and vibrations as well as ionizing radiation and vacuum. We develop and integrate laser systems and, in some cases, electronics to make novel measurements and processes possible, for example to create structures from regolith - always with a view to optimal space suitability with maximum reliability.
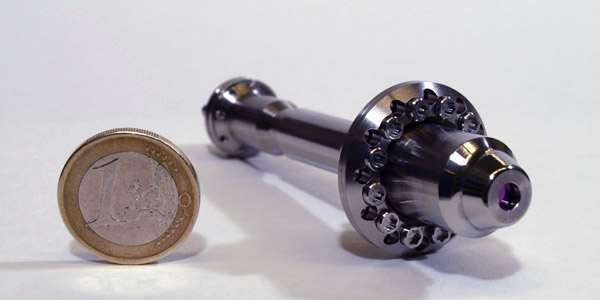
Laser-induced breakdown spectroscopy (LIBS) can be used to examine the atomic composition of material samples almost non-destructively. The laser must emit a high-energy pulse to generate plasma on the sample. We are constantly developing miniaturized Q-switched solid-state lasers to use this analysis method in the future to search for elements or water on planetary surfaces such as the moon.
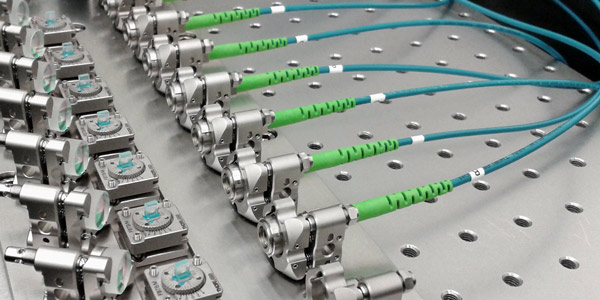
To enable purely optical communication networks in the future, we are working on laser amplifiers in the wavelength range between 1000 nm and 1100 nm. Laser-based communication is expected to increase data transmission rates by a factor of 10 to 100 to the terabit per second range. This requires satellites with laser terminals containing ten or more optical channels. We are working on a laser amplifier that can amplify all these channels simultaneously.
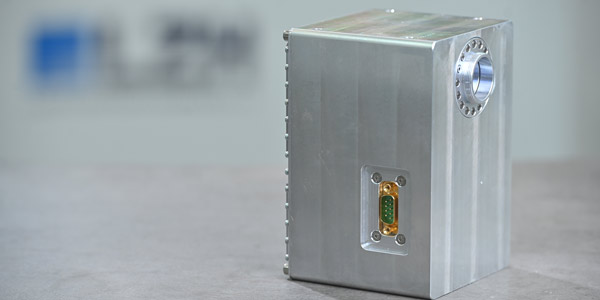
We design, develop and build suitable laser systems for 3D printing or additive manufacturing in zero gravity and under space conditions. In the future, this should make it possible to print tools, spare parts, or other components ad hoc on-site in space when they are needed. With our laser systems, we want to make it possible to melt the regolith there directly on the moon. This would be an essential step towards establishing manufacturing technology in and for space and a future outpost on the earth's satellite.
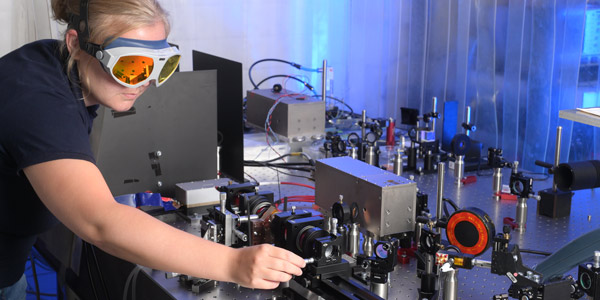
In the future, satellites with alexandrite-based LIDAR (Light Detection and Ranging) systems will monitor the health of vegetation on earth, generating valuable data on the state of our planet. We are working on laser systems for LIDAR applications with high output power that can withstand the harsh conditions of space. Alexandrite laser crystals have a tunable output wavelength and can thus select the most suitable wavelengths for measurement. Therefore, we are working with European partners to enable an all-European supply chain for space-qualified alexandrite laser crystals. We are also working on Q-switched lasers for altimetry, i.e., measuring the earth's surface or other planets, at 1064 nm and 532 nm, respectively.
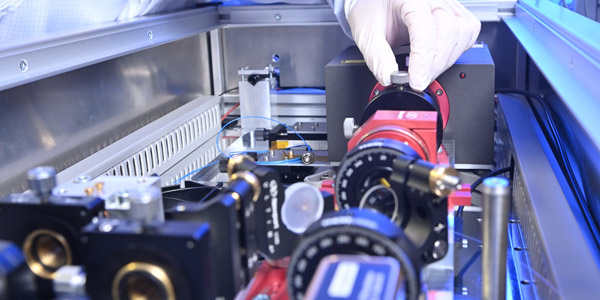
We have been developing crystal and later also fiber laser systems for gravitational wave detection for 30 years. The systems have already been used in earthbound gravitational wave detectors, laying the foundation for the 2017 Nobel Prize on the subject. These lasers must be highly stable, single-frequency, and fundamental-mode at 1064 nm. For even more reliable detection, we are working to further scale the performance of the systems. The next generation for ground-based detection is expected to reach a power of 500 W. At 1.5 µm wavelength, we aim to scale the power to 100 watts. For space-based gravitational wave detection, we are working on fiber amplifiers at 1064 nm.
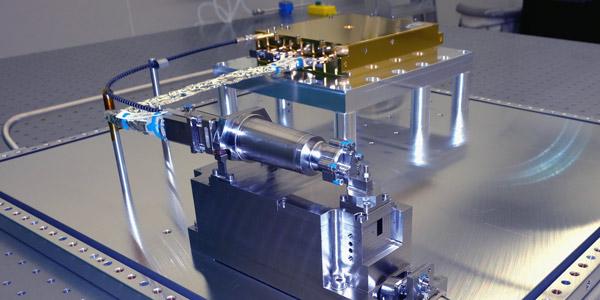
We have been developing pulsed ultraviolet lasers as part of the ExoMars mission since 2006 to search for traces of extraterrestrial life. Our lasers are used for the investigation of soil samples by laser desorption mass spectroscopy (LDMS) on Mars and enable the determination of organic molecules. For this they have to be lightweight and compact, and must be vacuum capable and vibration resistant. This technology can generally also be used to search for life on other planetary surfaces.
Technologies for flight hardware
With our laser laboratories and clean rooms, we have the necessary infrastructure to manufacture and assemble flight hardware for space missions. We develop smart manufacturing technologies to further maximize hardware reliability and robustness to contribute to successful space missions. We have already successfully delivered our hardware to ESA and NASA.
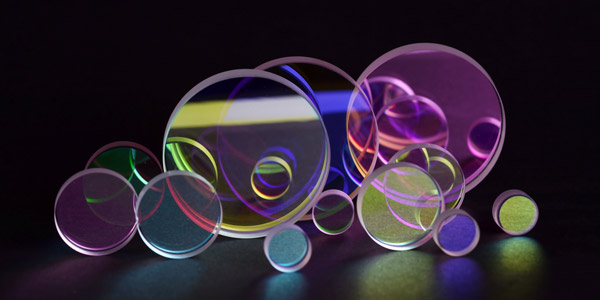
We design and optimize special coating systems for telescopes on earth and in space. We work on broadband and narrowband filters for highly accurate and sensitive measurements. With our high-precision ion beam sputtering (IBS) systems, we can coat large optics with a circumference of up to 500 mm for high-resolution telescopes. We also develop robust coatings for particularly durable laser components and high destruction thresholds so that telescopes do not fail at the crucial moment.
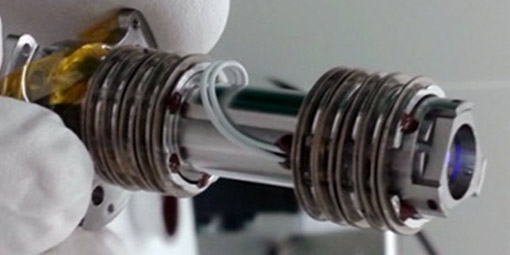
Lasers for use in space must be filled with artificial air and hermetically welded to protect the optics inside. Adhesives are not suitable for mounting technology inside because they outgas and then contaminate the optics. We optimize clamping and soldering processes that enable extremely precise contamination-free assembly and thus contribute significantly to long laser and thus instrument lifetimes.
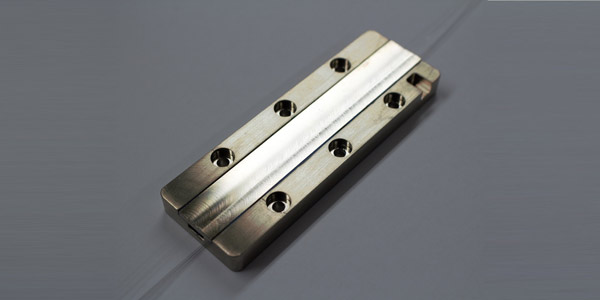
For the use of fiber laser systems in space, the individual components must also be designed to be space-qualified. We design and manufacture end caps, cladding light strippers, mode field adapters, pump combiners, and wavelength division multiplexers to qualify them for use in space. Furthermore, we are working on standardizing and continuously optimizing the manufacturing of fiber components through automation.
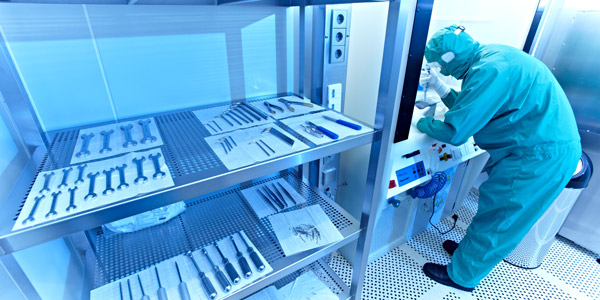
For long laser lifetimes and high reliability, it is essential to protect the individual optical components from contamination, i.e. from particulate and molecular impurities. To this end, we operate clean rooms equipped with special filter technology and have optimized our work processes and environment to meet these very high requirements. We have developed special cleaning processes for components and contamination monitoring for quality control, thus achieving very high standards.
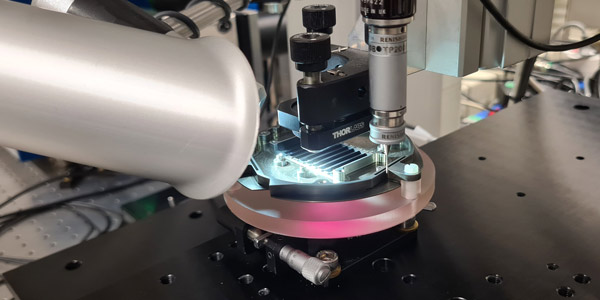
Ultra-short pulse lasers have enormous potential for processing components for flight hardware: From sample production for experiments in microgravitation to anti-reflective structures on surfaces of optics for the millimeter wavelength range to microcomponents made of a wide variety of materials for measuring devices in satellites. We are continuously optimizing the machining processes and techniques for process control and characterization of the results to constantly open up new applications and provide a custom-fit solution for every requirement.
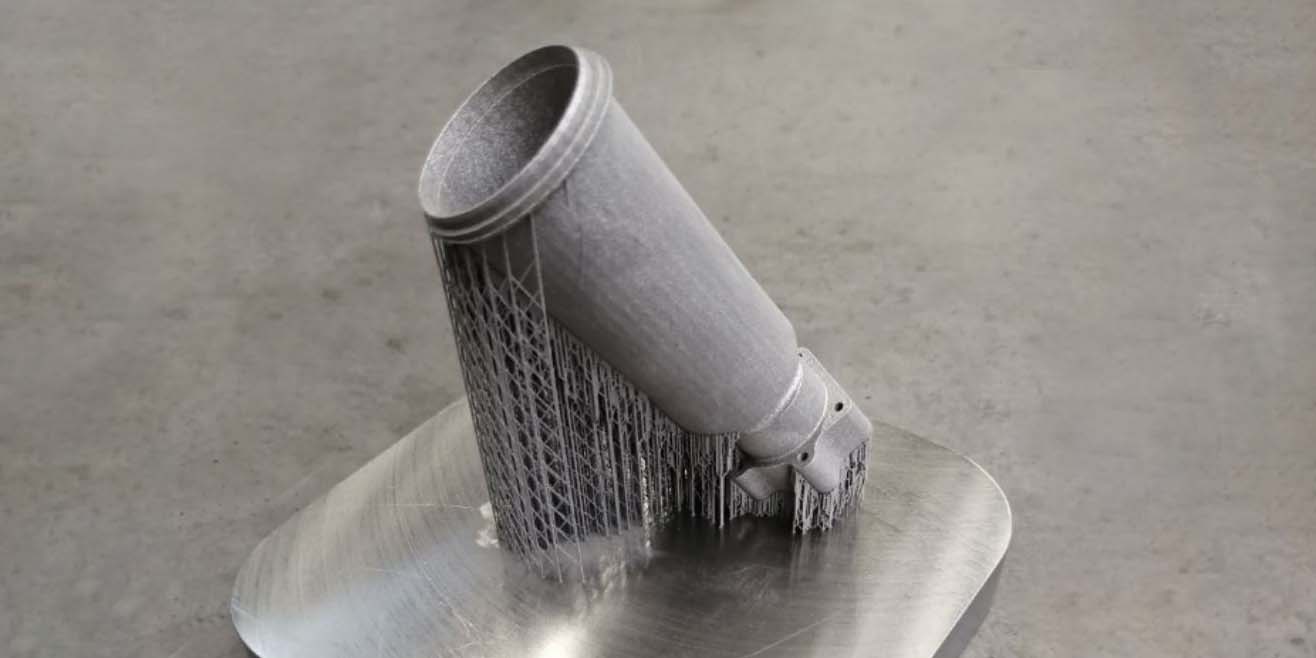
If components cannot be manufactured using classic subtractive processes, we use Additive Manufacturing or a combination of both processes. With powder bed processes, we can produce very robust metal components. In the components, we integrate new functions such as mounting devices to optimize the interaction with other components. We also use topology optimization to save material and thus weight. Depending on the intended use, there is a choice of different materials, such as titanium, which is very interesting for space applications.
Qualification
The success of entire space missions also depends on the reliability of the components and their assembly. Therefore, we implement quality management and accompany the development of components and laser systems from the very beginning. We test and optimize small-step design and function of components and assemblies up to the flight model, for utmost reliability and short development time.
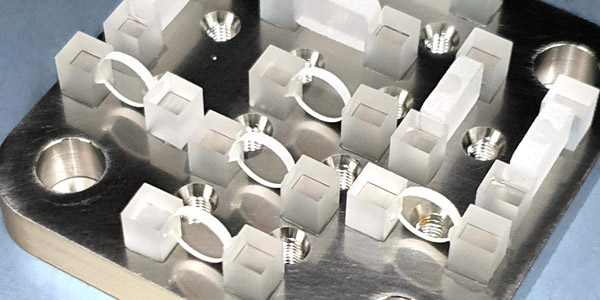
To prove the desired specifications of individual components or entire laser systems, meaningful tests must be planned. Launches and landings can cause strong vibrations. The hardware must be radiation resistant, withstand thin atmospheres or even vacuum and wide temperature ranges. We review the requirements of the planned mission and design the tests accordingly to ensure subsequent functionality. We are constantly developing and optimizing our test capabilities to meet the increasingly complex systems and mission requirements.
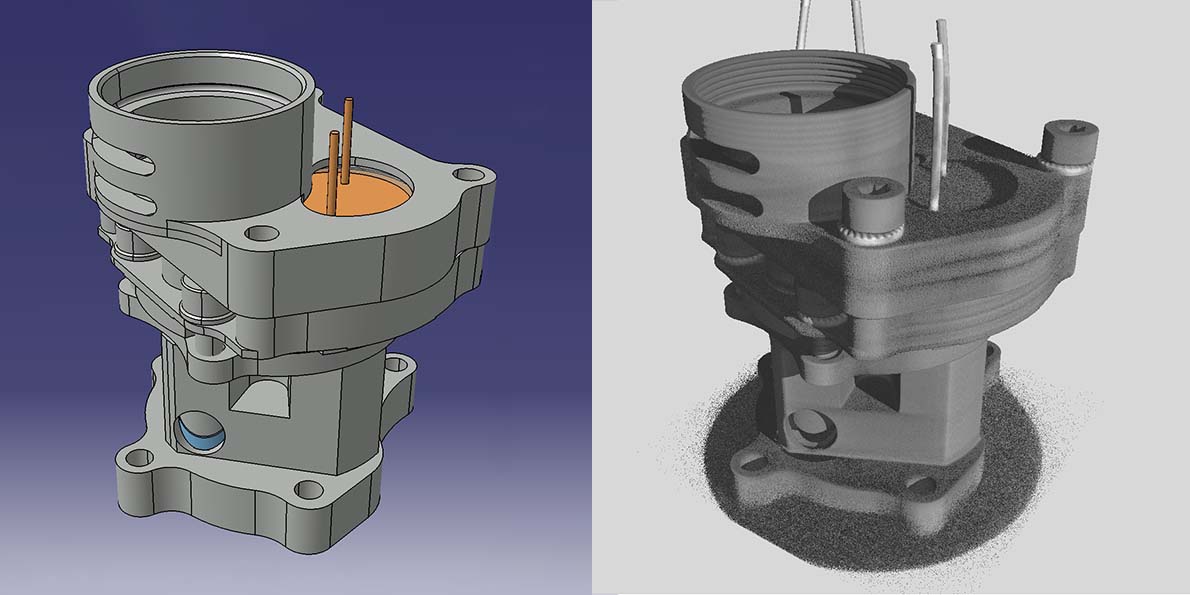
We examine the assembly of lasers and other systems non-destructively in the 3D X-ray tomograph. In doing so, we check whether all components have been assembled correctly. We also examine the hardware for possible damage using computer micro-tomography (µCT) after environmental tests. Internal defects, such as the smallest cracks or damaged areas, which could lead to equipment failure in space, are thus revealed in good time.
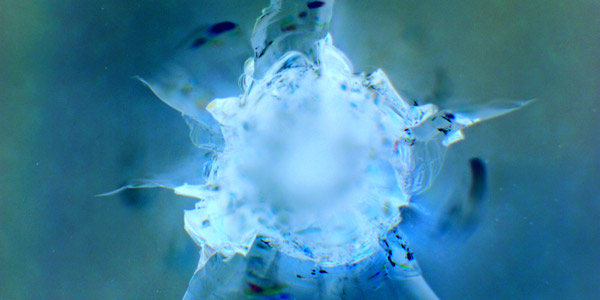
Contaminated optics or improperly designed optics can prematurely and unintentionally terminate measurements in space. Damage during operation can reduce reflectivity and transmission to such an extent that the system's lifetime decreases enormously. We test and qualify optics using laser-induced damage threshold (LIDT) measurements, laser-induced contamination (LIC), and laser absorption, always using state-of-the-art methodology. These results provide essential information for optimally adapting and designing future optics to environmental conditions, such as volatile substances for printed circuit boards or insulation materials. With the growing requirements, we also continuously develop our qualification methods.
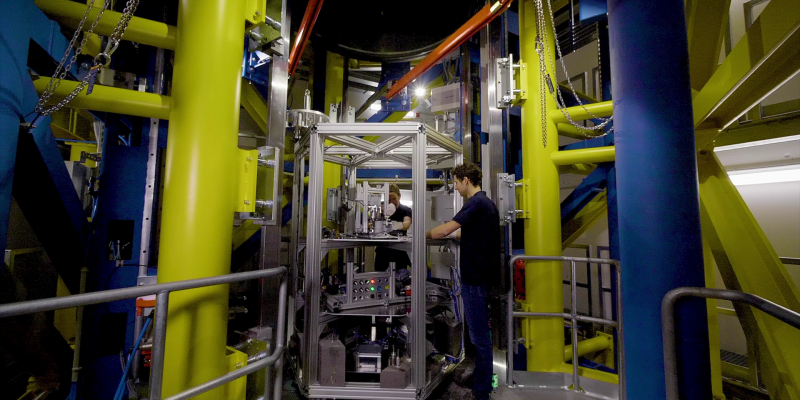
In the Einstein Elevator at the HITec in Hannover, we can easily perform tests under different gravitational conditions. With this unique further development of a classical drop tower, it is possible to perform experiments under conditions of microgravitation but also under Mars or moon gravity. The high repetition rates of this elevator allow us to obtain statistically very significant results. Thus, the influence of changed gravitational conditions on experiments such as additive manufacturing or laser material processing can be investigated. This unique large-scale research device enables us to test our systems or innovations in an uncomplicated way under space conditions and thus realize fast innovation cycles in space research.
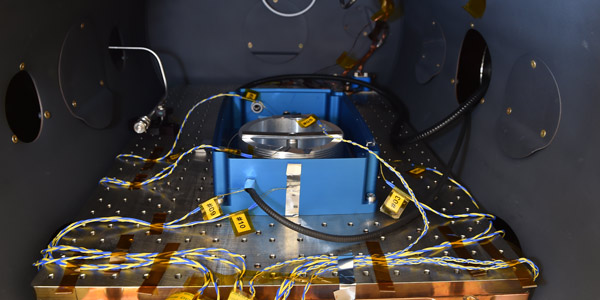
We have a range of measuring equipment available for in-house environmental testing to put components or entire laser systems through their paces. In our thermal vacuum chambers, we can test hardware at temperature cycles between -70°C and +150°C to see if it can withstand temperature variations typical of space missions. The chambers are equipped with optical windows and are operated in the laser safety range. Therefore, we can perform active or passive tests to ensure functional capability in space. We use vibration tests to verify that components and systems can withstand severe shaking during rocket launch and landing. We continuously adapt our methods to the current standards (of ESA/NASA) and always test our space systems with the best possible methods.
Production technology in space
Working directly in space with raw materials available there, for example to manufacture or repair components or structures - that's what we're researching. We are transferring our knowledge of production technology to the conditions in space, thereby expanding our understanding of the fundamentals. Among other things, the Einstein elevator is available to us for this purpose.
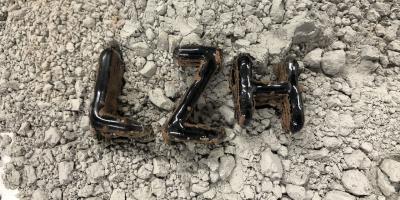
Transportation from earth to space is costly. Additive manufacturing of components and structures with raw materials available on-site would open new possibilities for building infrastructure or other elements. We are developing processes for laser fusion welding of lunar dust (regolith) to manufacture functional structures and components on the moon in the future. To this end, we are conducting experiments under lunar gravity or microgravitation in a specially developed capsule in HIiTec's Einstein Elevator to simulate real conditions in space as closely as possible and thus establish validated technologies for tomorrow's space missions.
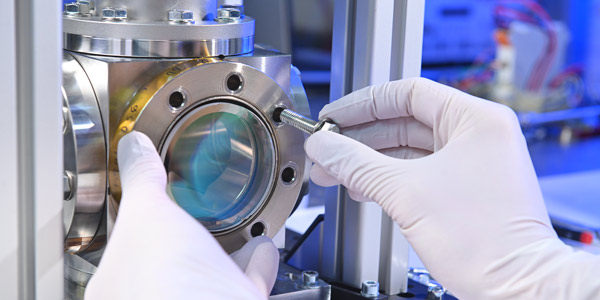
Joining components directly in space or on planets will be unavoidable in the future. Further research into metal processing and welding technology, in particular, is therefore currently essential for extraterrestrial production technology. Consequently, we are investigating laser beam welding under different gravity conditions in the Einstein Elevator. For this purpose, we first examine the joining of geometries. We will then transfer the fundamental knowledge gained here, such as the behavior of the molten pool, to initial components and further materials and joining processes to optimize the process for the requirements of production in space.