LASER - World of PHOTONICS 2023: Additive Manufacturing
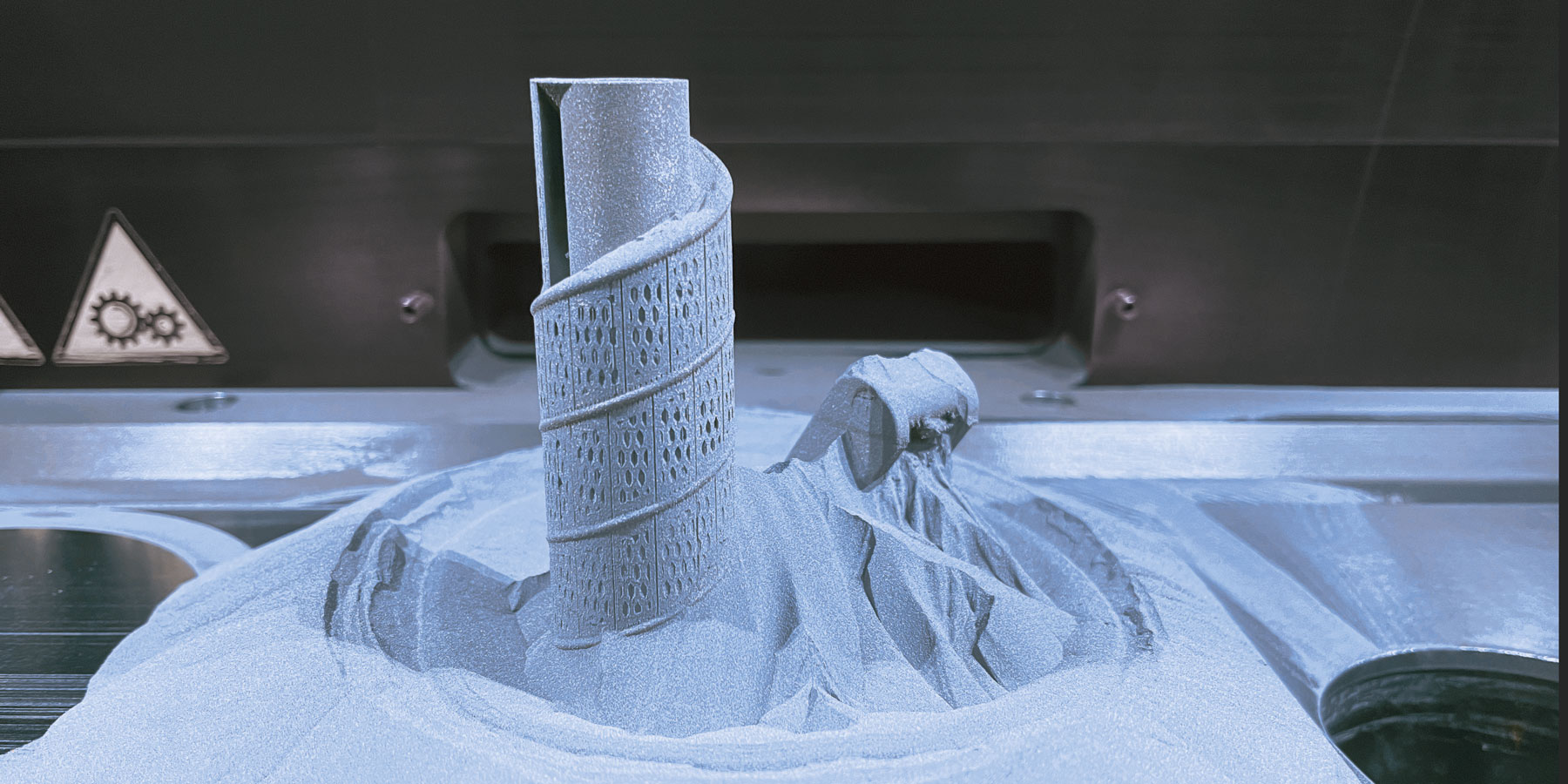
Contact
Phone: +49 511 2788-419
Email: messe@lzh.de
Fabrication of Magnesium WE43
Advantages of magnesium
• Lightest construction metal
• Highly biocompatible
• Biodegradable
Applications:
• Implants
• Lightweight structural material
Drawbacks of Magnesium
• Unstable processing behavior
• Reactive material: a strong oxidative tendency
• Necessity for specialized machines
Stabilizing the melting process
• Hydrogen in inert gas for maximizing remaining oxygen in the process
• Improving the air circulation for less interference of processing gases with laser beam
• Different laser source to optimize energy transfer in powder bed
• Higher build plate pre-heating for in-process stress reduction
Processing of novel magnesium alloys
• Tailored magnesium alloys to reduce oxidation (WE43, MgSrY, and ZX00)
Increase in economy of the additive magnesium fabrication
• Improvement in build-up rate by 230% (increased layer height by 100 %, 20 µm)
Process monitoring of spectral emissions
• Digital twin of fabricated parts --> prediction of material properties
Parameters of current WE43 Demonstrators
• PBF-LB system: SLM Solutions SLM125HL
• Material: WE43
• Laser power: 100 W
• Scanning speed: 400 mm/s
• Hatch distance: 60 µm
• Layer height: 40 µm
→ 100 % relative density
→ sub 150 µm structure width
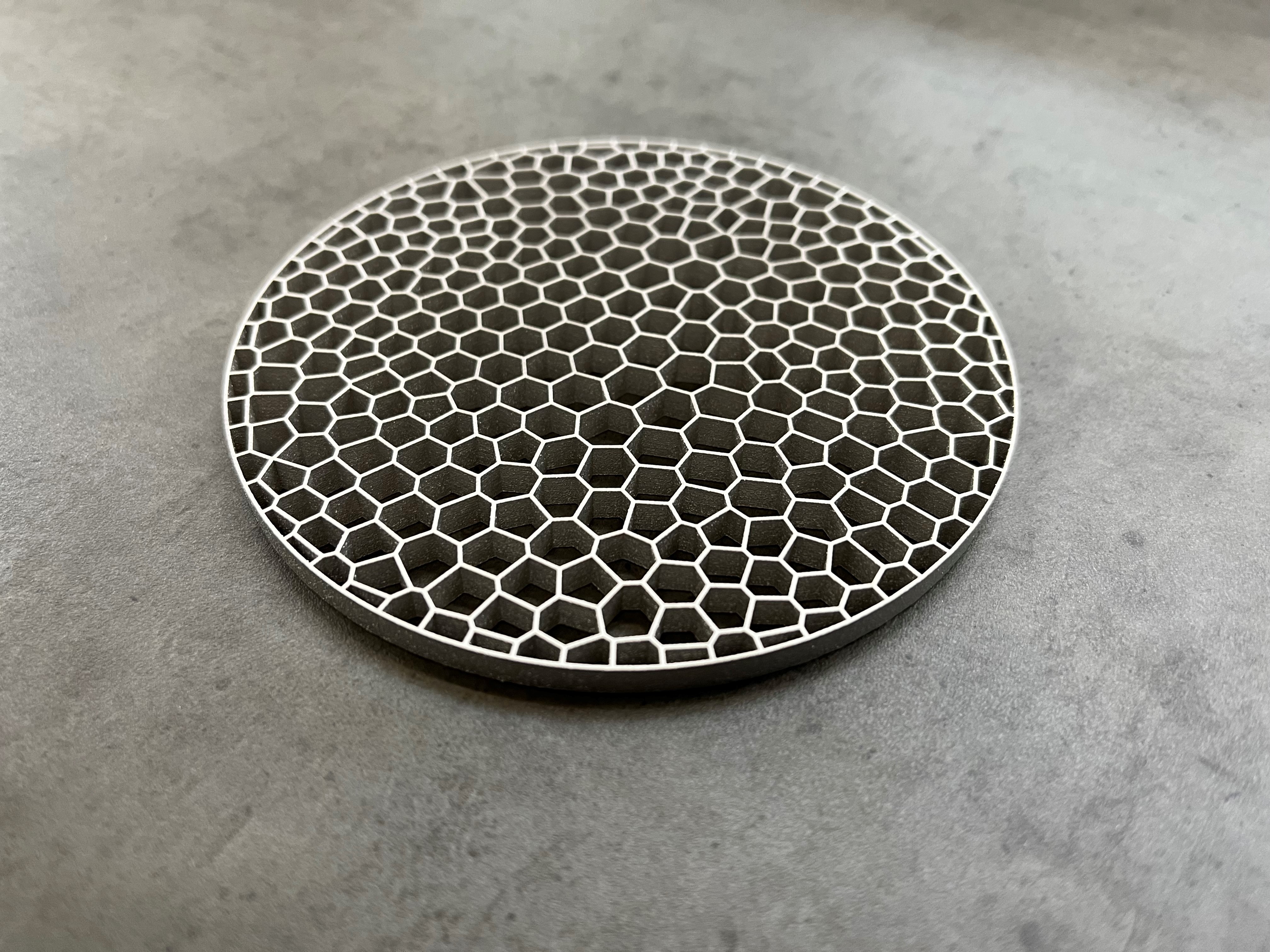
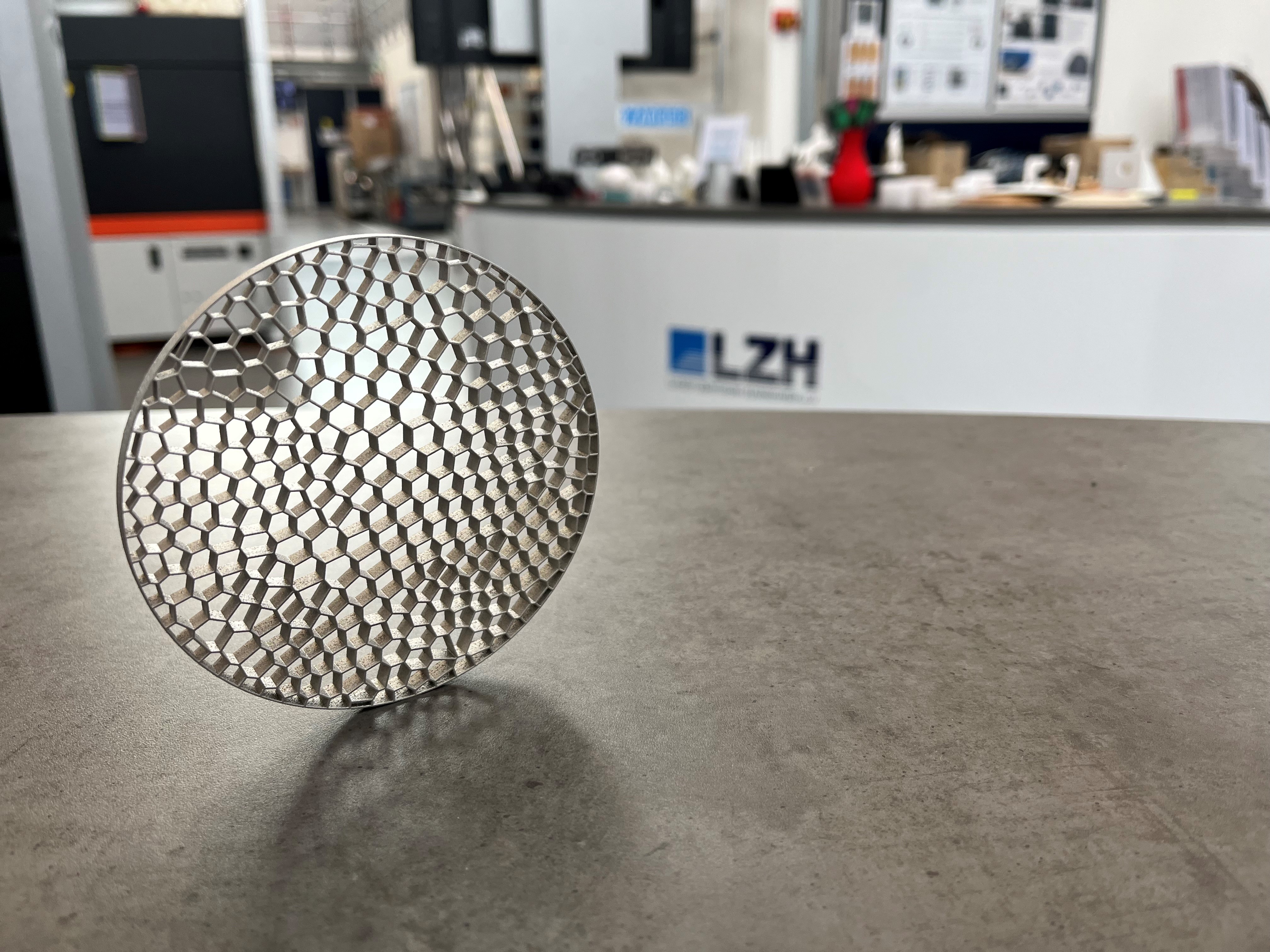
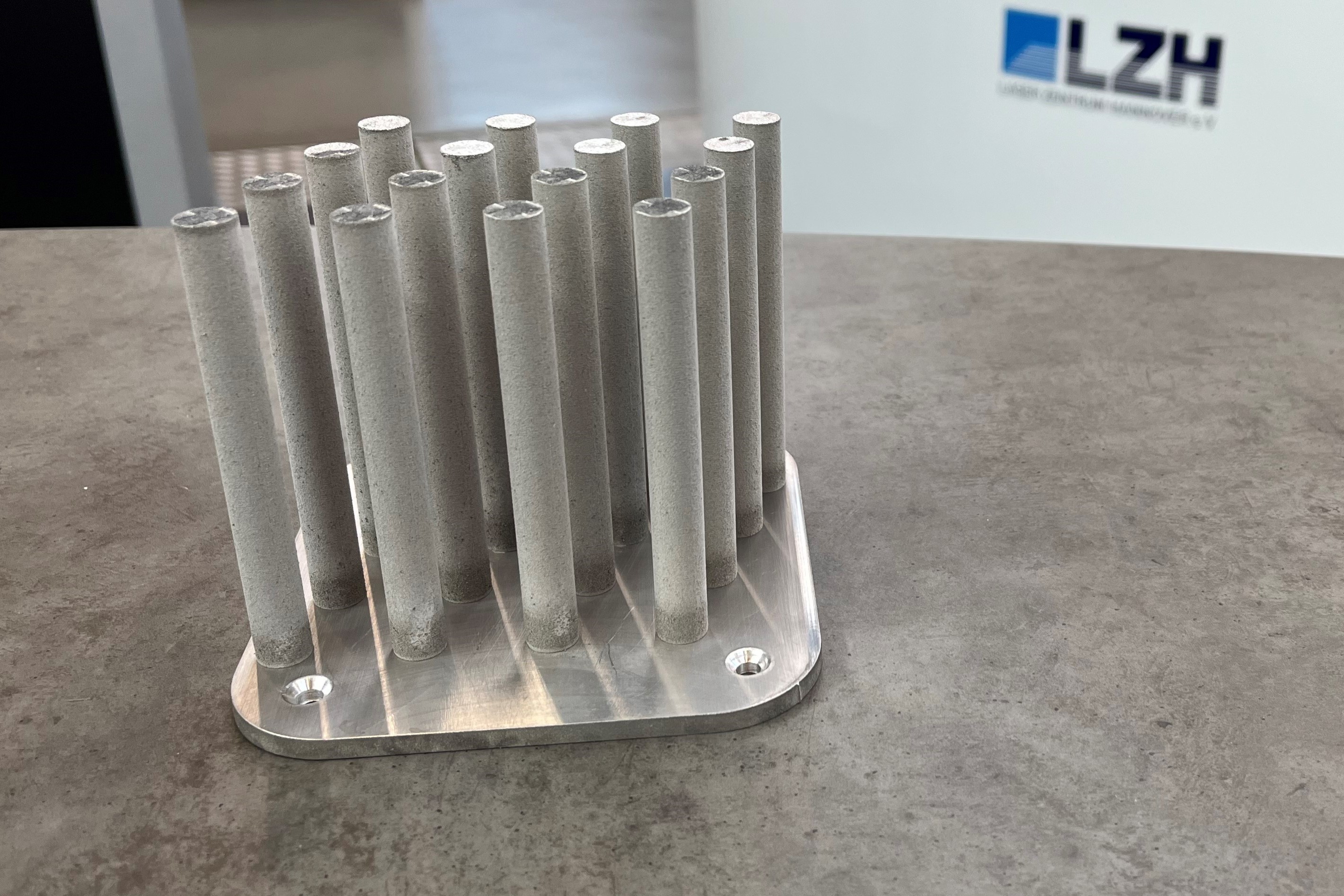
Glass
Motivation
• Limited flexibility for conventional glass processing
• Novel glass components by 3D free form design
Function/Properties/Characteristics
• Monolithic material bond
• High transparency, no bubbles, and defects
• Low surface roughness
• No surface polishing
Applications
• Free-form optics and new optical functionalities
• Complex glass components with undercuts for chemical engineering
• Punctual holder in glass facades to substitute adhesive joints
Parameters
• Laser power = 110 W
• Feed rate = 270 mm/min
Laser sources
• Diamond Coherent J3
• CO2 - Laser
Processed material
• Substrate: Fused silica (3 mm thickness)
• Additive material: Fused silica fiber (0.4 mm thickness)
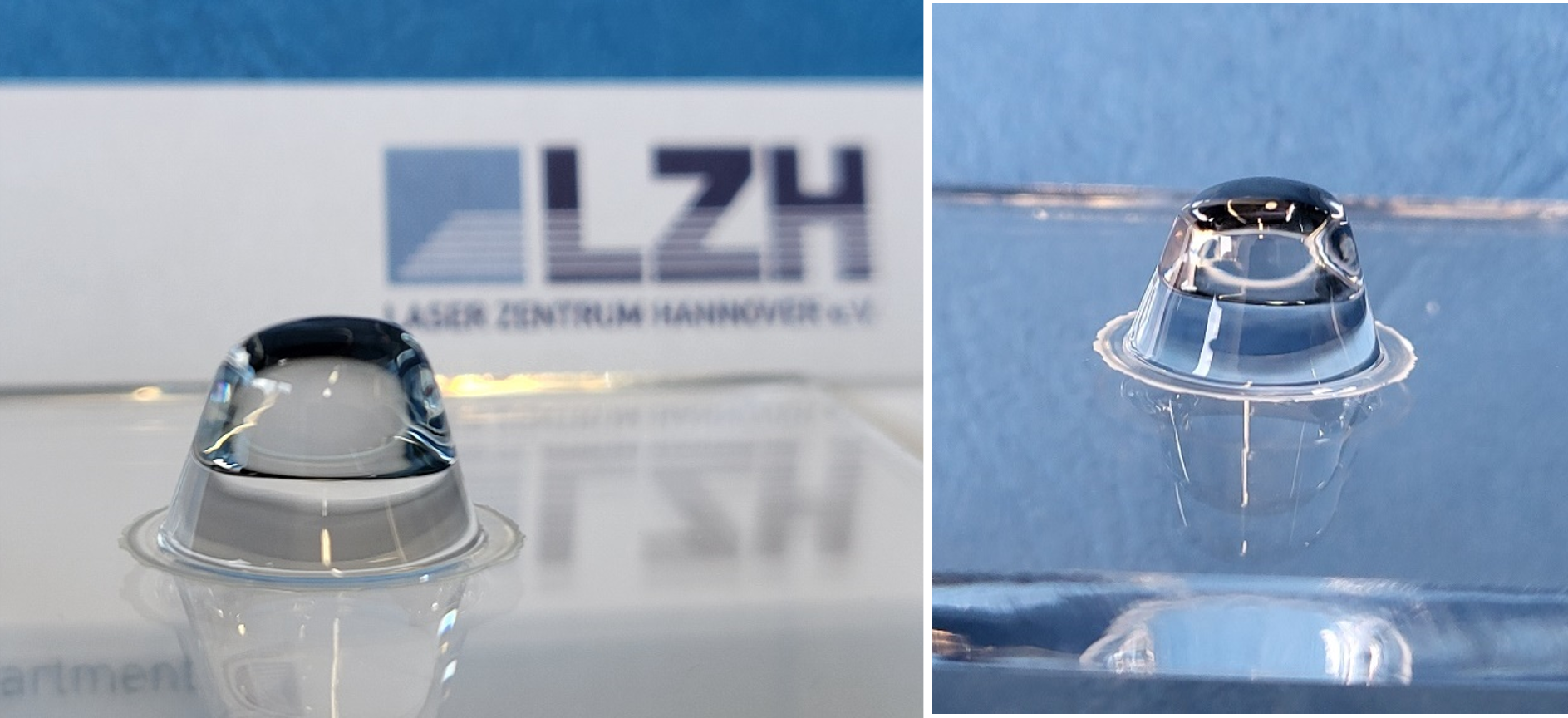
Biocomposites
Motivation
• Exploiting FDM 3D printing with sustainable materials from renewable resources for large-scale architectural components
• Design and fabrication of 3D printed components from biocomposites/filaments with continuous and short natural fibers
Function/Properties/Characteristics
• Interior facade elements
• Material: PLA with 20 % wood short-fiber
Applications
• Architectural components
• Production of facade elements in the exterior and interior
• Production of segments for the construction of a pavilion
Parameters
• Total dimensions: 300 x 300 x 60 mm³
• Layer height: 0,40 mm
3D-Printer
• ATMAT Saturn FFF-Printer
• Buildvolume: 1200 x 1000 x 1000 mm³
Processed material
• PLA with 20 % wood short-fiber
The showcase model is merged out of four tiles and is scaled down to 300 x 300 mm instead of 400 x 400 mm. The original demonstrator consists of 16 tiles with dimensions of 200 x 200 mm each with a total dimension of 800 x 800 mm.
Goal:
• Development of FFF 3D printing with sustainable materials from renewable resources for large-format architectural components
• Process development for FFF printing of continuous fiber-strengthened biopolymers
• Development of a suitable print head for printing continuous fiber reinforced filaments
• Development of a cutting mechanism in the print head to separate the continuousfiber filaments
• Production of facade elements for exterior and interior applications
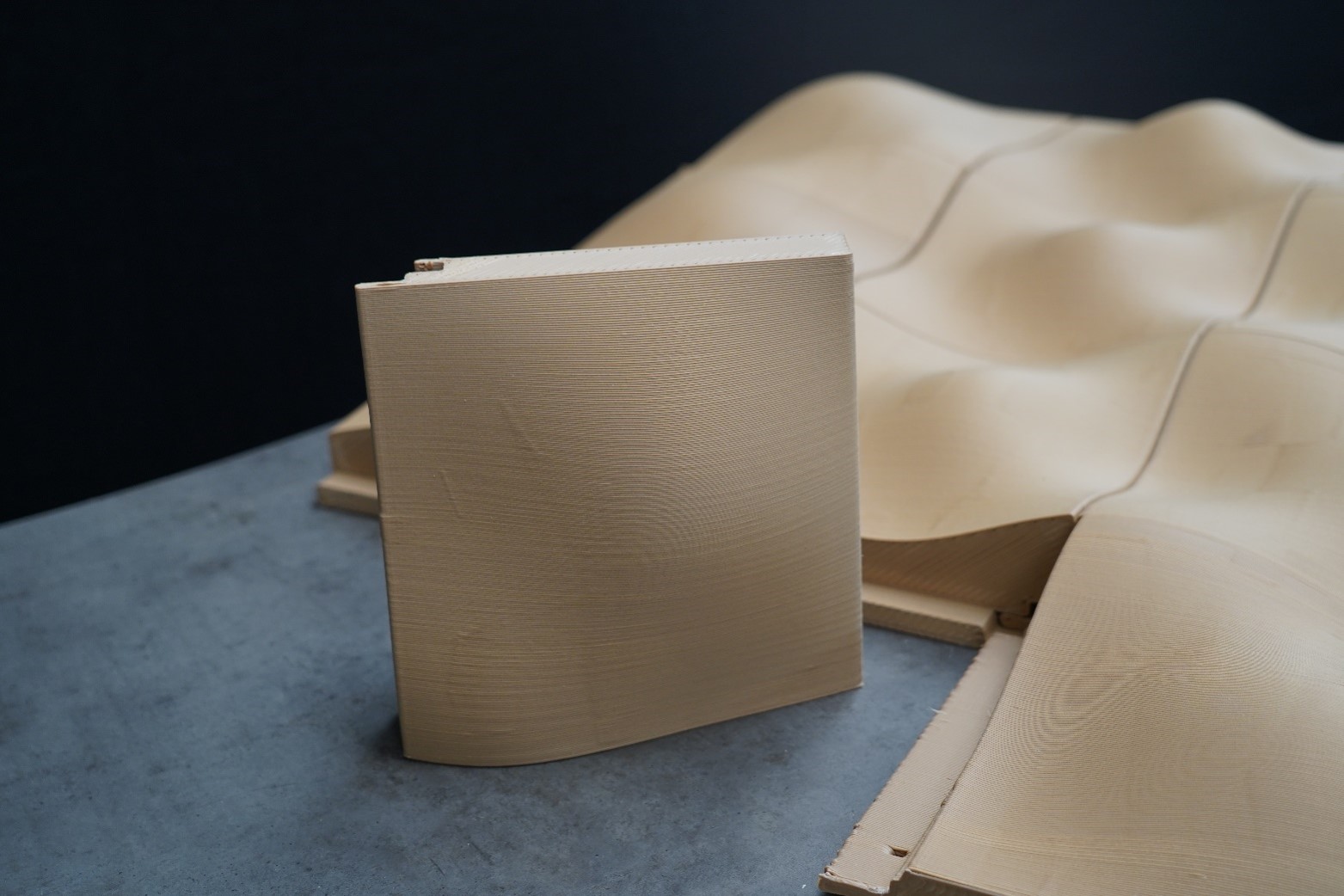
Micro-Components
Micro drill with integrated closed cooling loop
Motivation
Up until now, it was not possible to integrate closed cooling loops into micro drills. The LAMµC technology enables the production of complex internal structures with diameters of up to 100 µm. Thanks to integrated cooling, it is possible to drill deep into the bone without causing tissue damage due to heat dissipation.
Function
The exhibited micro drill is a prototype for applications in medical technology, e.g. for minimally-invasive surgery. The closed design prevents contamination of the surgical area by cooling fluid. The micro drill shown is made of 1.4404; the diameter of the channels is 200 µm.
Applications
• Minimally-invasive surgery
• Otorhinolaryngology
• Endodontics files
Hybrid additive series production
Motivation
A significant cost factor in additive manufacturing is the long processing time. LAMµC pursues a hybrid production approach to make additive series production of micro components even more efficient. By printing directly onto semi-finished products, production times and costs can be significantly reduced.
Function
LAMµC uses a clamping technology that enables over 850 semi-finished products to be clamped simultaneously with an accuracy of 3 µm. The clamping technology can be customized and enables efficient and precise production. Due to the fully automated process, very high quantities can be produced at high quality.
Applications
• Series production of micro components
• Hybrid manufacturing
• Integration of semi-finished products
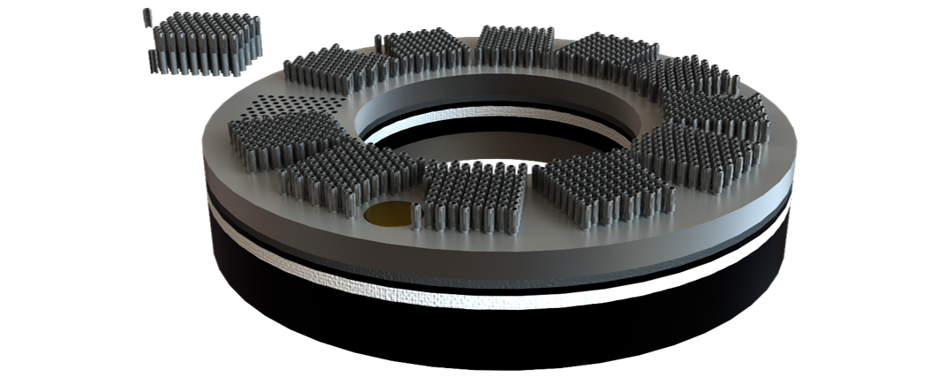
Micro boring rod
Motivation
A major challenge in micromachining is cooling close to the cutting contour. Due to its unique ability to produce complex micro-cooling channels, the LAMµC technology is ideal for the manufacturing of customized micro boring rods.
Function
The boring rod shown is manufactured hybridly on a 3 mm precision shaft. The diameter of the cooling channel is 200 µm. Due to the hybrid additive approach, micro boring rods can be manufactured cost-efficiently and precisely using the LAMµC technology.
Applications
• Micromilling
• Microdrilling
• Microturning
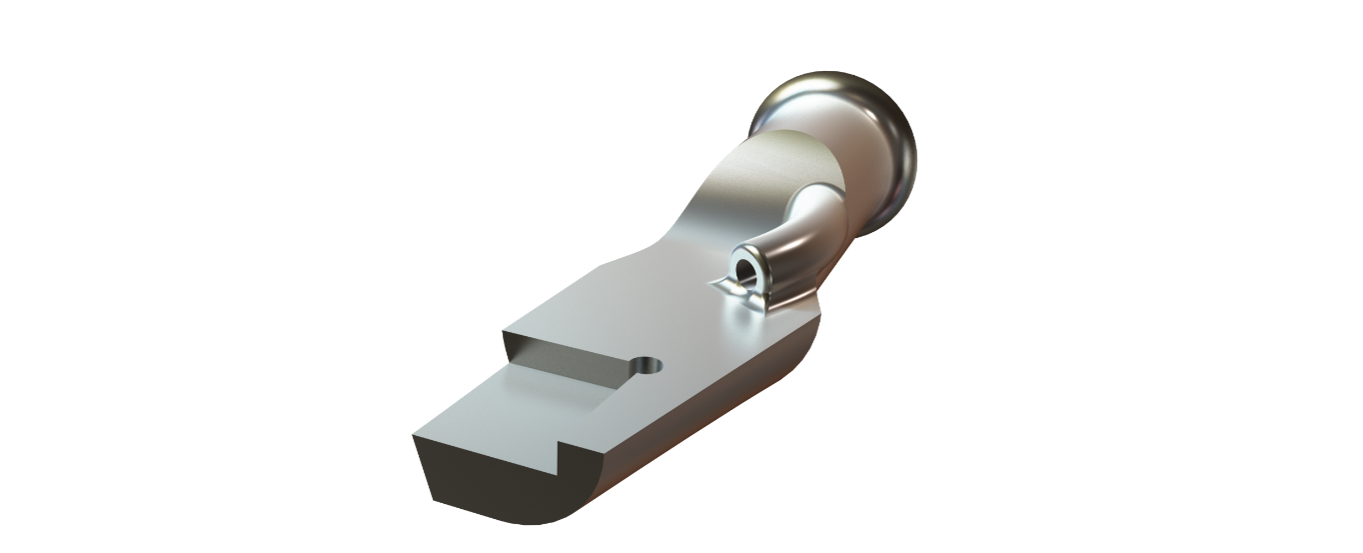
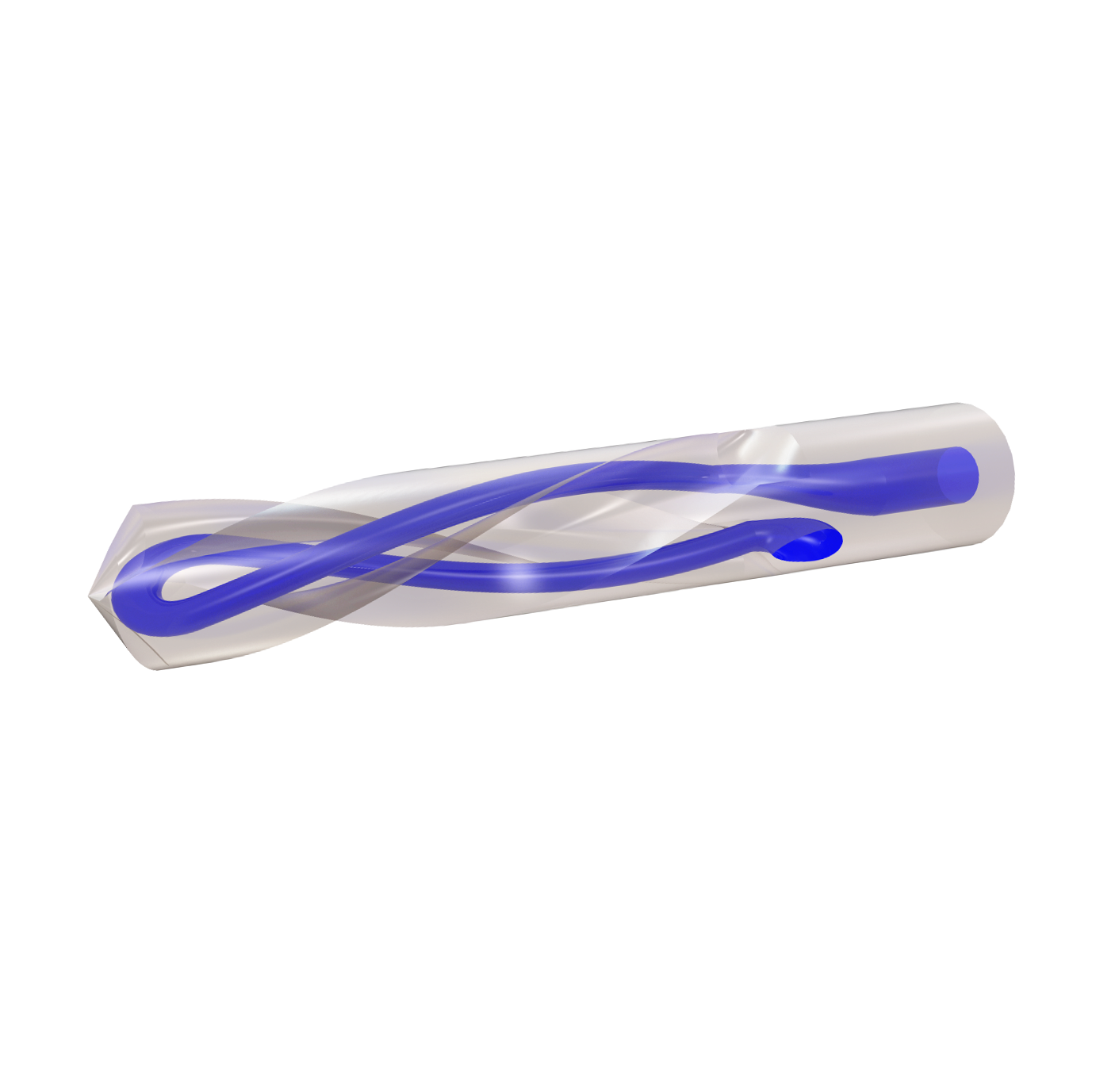
Hydraulic valve
Motivation
In small and medium-sized companies conventional prototyping of hydraulic valves often occupies CNC-machining centres of the series production line. Here, powder bed fusion by laser beam (PBF-LB/M) offers production flexibility due to its highly automated additive manufacturing process based on 3D CAD files. Layer by layer, prototypes can be iteratively developed into series products. This does not require any major adjustments to the production line. Compared to conventional production processes, the design of components is almost limitless. Components can be printed in a topology-optimized way, with integrated structures and functions. This saves printing time and material. Weight reductions, more efficient cooling and the selection of a wide variety of materials ensure greater productivity and energy savings for additively manufactured components in later applications.
Function / Properties / Characteristics
• 150 bar operating pressure (tested)
• 27 h build time
• 435 g -> 69 % weight reduction
Applications
• Agricultural sector (control valve e.g. for seed drill)
Parameters
• 110 W laser power
• 750 mm/s scan speed
• 20 µm layer thickness
Laser sources
• cw ytterbium fibre laser, 1070 nm
• 30 µm spot size
Processed material
• stainless steel AISI 316L (1.4404)
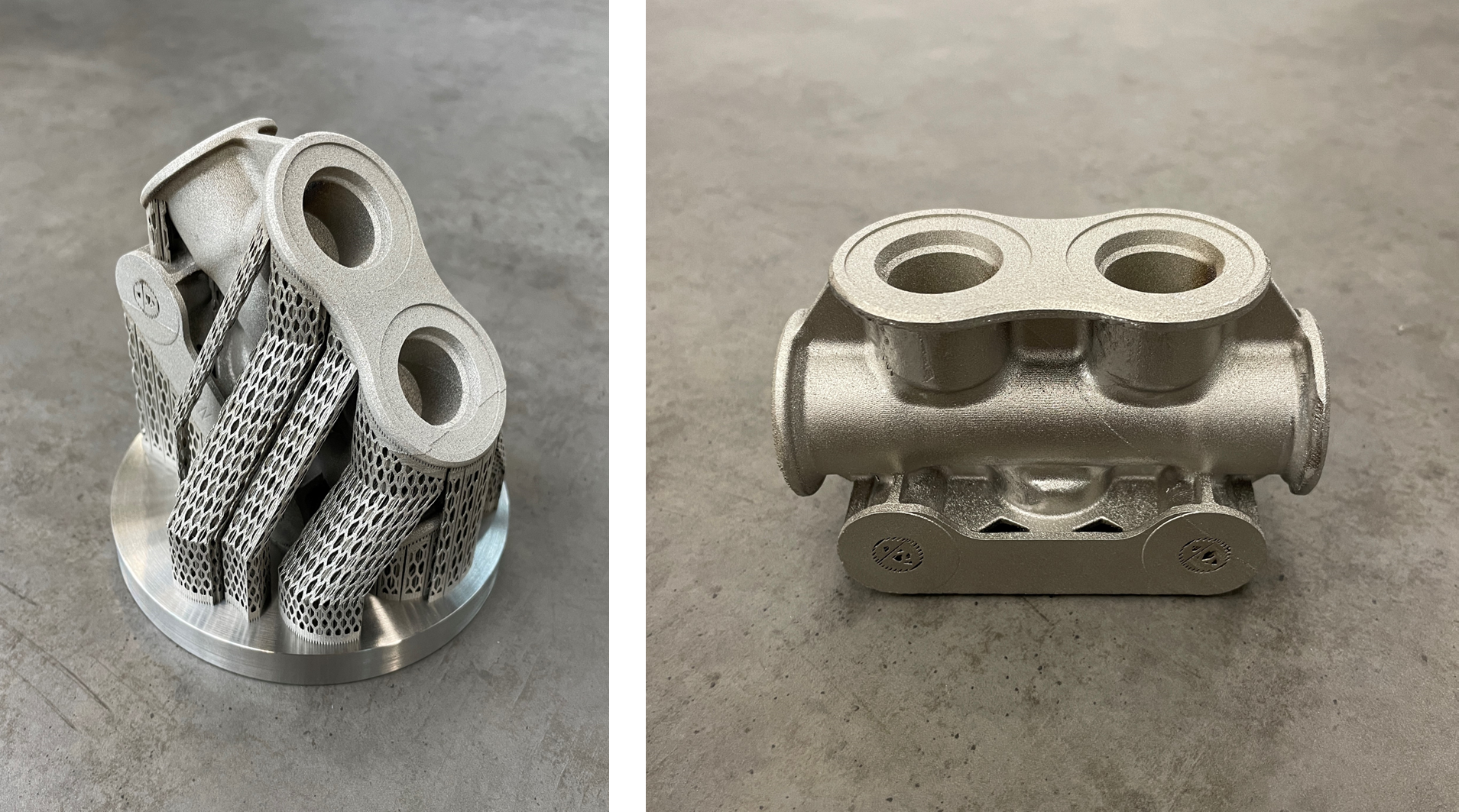
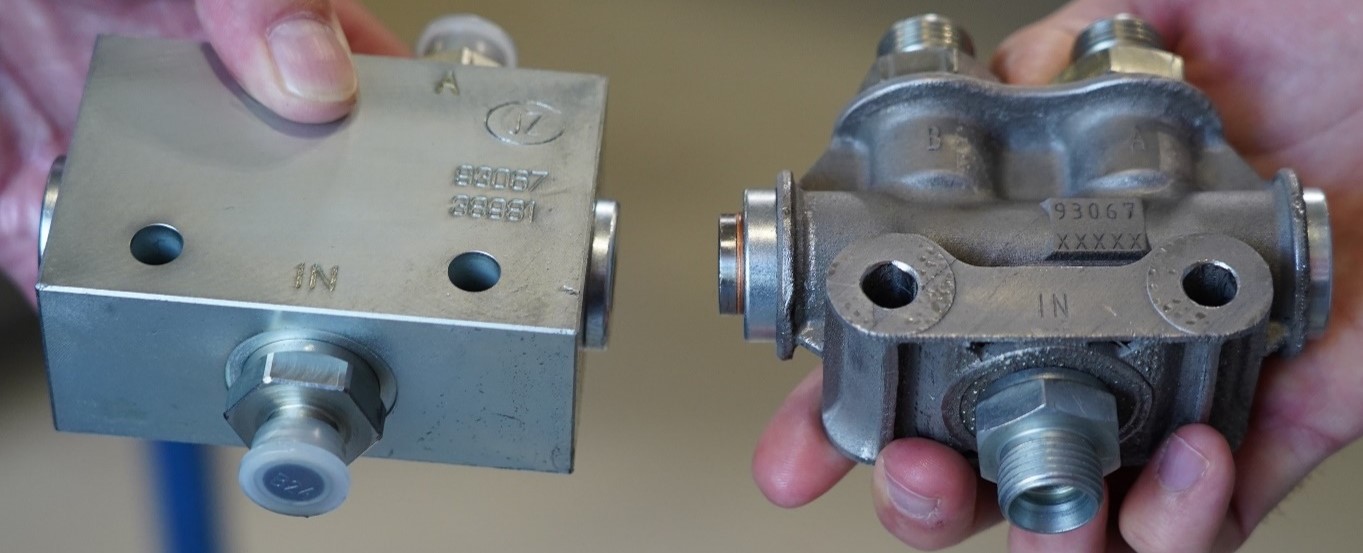