LASER - World of PHOTONICS: Laser Material Processing
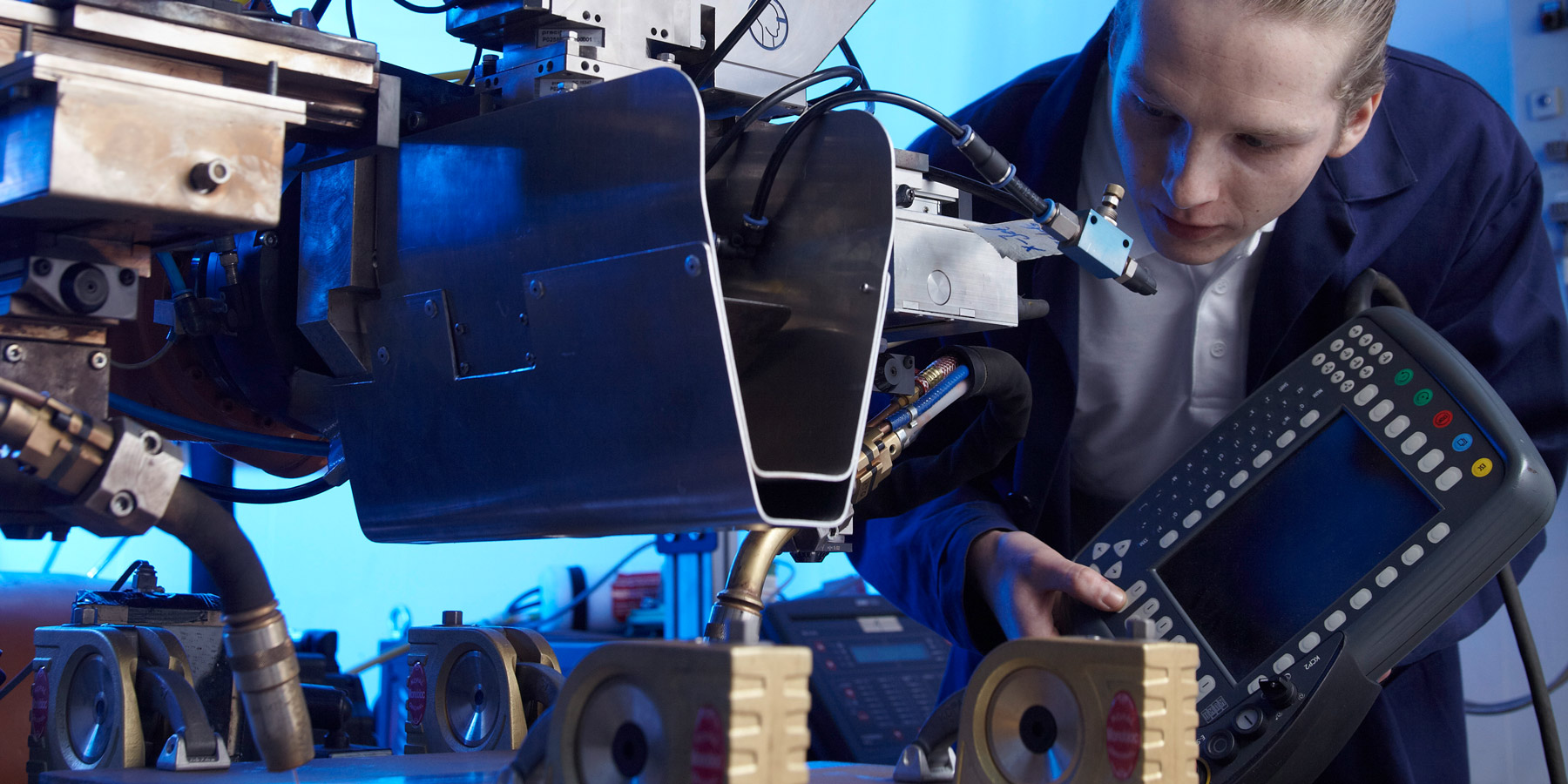
Contact
Phone: +49 511 2788-238
Email: messe@lzh.de
Steel and aluminum
Motivation
• Lightweight construction in shipbuilding to reduce CO2 emissions and increase ship stability
• Alternative to joining of steel with aluminum by explosion welding (complex, time-consuming and cost-intensive joining process)
• Low strength → oversizing and low design freedom of explosion-welded joints
Properties
• High potential for efficient laser beam welding of form-fit dissimilar joints of steel and
aluminum with high strength → no oversizing → higher design freedom
• Generation of an undercut by two-sided, crossing laser beams
• increase the deformability and strength under head loading
• Combination of form-fit and material-fit
Applications
• Shipbuilding (Connection of steel hull and aluminum superstructure by means of adapters)
• Wagon construction
• Scaffolding construction etc.
Parameters
• Laser power: ≈ 6 kW
• Welding speed: ≈ 1,0 m/min
• Angle: ≈ 15 – 45°
Laser sources
• HighLight FL6000-ARM (COHERENT, INC.)
• Fiber Laser
• ARM: Adjustable Ring Mode
Processed material
• Steel S355 (t = 5 mm)
• Aluminum alloy AA 6082 (t = 8 mm)
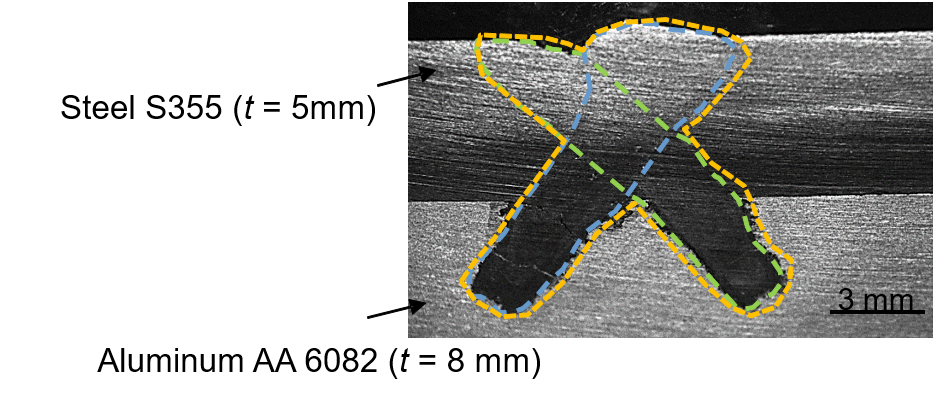
Ultrasonic laser beam welding
Motivation
• Joining dissimilar metals (nickel base metal + stainless steel, 41Cr4 + C22.8)
• Ultrasonic intermixing and reduction of segregation and cracks during laser beam welding
• Ultrasonic grain refinement during laser beam welding
Function / Properties / Characteristics
• Standing wave and weld positioning in node or antinode
• Solid bar diameter: 30 mm
• Hollow bar outer/inner diameter: 40/16 mm
Applications
• Round solid and hollow bars
• Shafts
Parameters
• Welding power: 8 kW
• Welding speed: 0.95 m/min
• Defocussing: -4 mm
• Ultrasonic frequency: 20 kHz
• Ultrasonic vibration amplitude: 0-10 µm
• Welding at the ultrasound‘s nodal or antinodal position
• Clamping pressure: 20 bar
• Laser source: TruDisk16002
Processed material
• Nickel base alloy + stainless steel
• 41Cr4 + C22.8
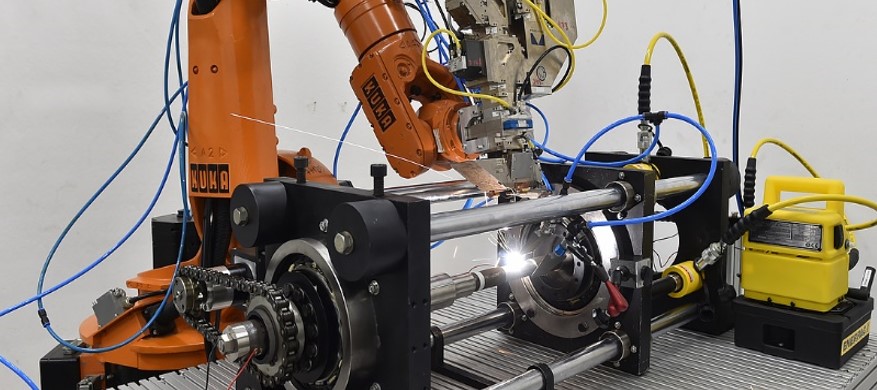
Thin-film sensors
Motivation
• Improvement in the performance and robustness of large engines by condition monitoring
• Integrated sensors and digital systems enable condition-based maintenance, reduction of downtime, and prevention of wear or damage by appropriate control strategies
Characteristics
• Bearing shell with laser patterned thin film strain sensors
• A wear protection layer embeds the sensor system to prevent damage from abrasion
• The sensors measure deformation and temperature in close proximity to the oil film between
journal and bearing during operation of the engine
Thin Film Deposition
• Dielectric isolation layer
• Sensor layer
Laser Patterning and Trimming
• Selective film removal by laser ablation / 3D surfaces
Connecting and Embedding
• Soldering / Wire bonding
• Additional protection layer or encapsulation
Thin Film & Laser Technology
• Flexible patterning process for 3D surfaces
• Highly integrated: Thickness less than 10 µm
• Thin film system deposited directly on surface: Robust, low drift, high temperatures
• High-precision resistor trimming process, tolerance < 0.1 %
Applications
• Force and stress measurement on components (3-D surface)
• Example applications: precision measurement on force-translating components, sensor
technology, thin-film electronics on component surfaces
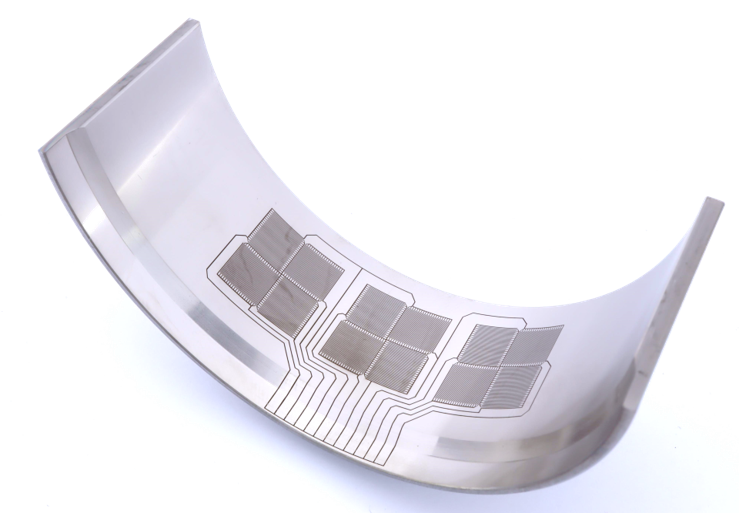
Drilling of CFRP
Motivation
• >150 000 000 drilling operations performed per year in the german aviation industry
• High tool wear when machining CFRP with drill bits
• High quality and high accuracy required
Function / Properties / Characteristics
• No tool wear with laser drilling
• Flexibility in bore diameter and drilling pattern without tool change
• Multi-material stacks drillable
• High quality and high accuracy:
• Heat affected zone <40 µm, drilling without taper achievable
Applications
• Macro drilling:
• High quality rivet hole drilling
• Micro drilling of large surfaces:
• Noise reduction & sound design in aerospace / automobile / construction industry
• Flow control / boundary layer suction
Parameters
• Remote processing
• Stepwise material ablation
Laser sources
• Nanosecond-pulsed high-power laser by TRUMPF
Processed material
• Carbon fiber reinforced plastics, Glass fiber reinforced plastics, CFRP-Sandwich materials
• Multi-material stacks drillable (e.g. thermoset CFRP laminate with thermoplastic laminate
including GFRP protection layer and copper mesh)
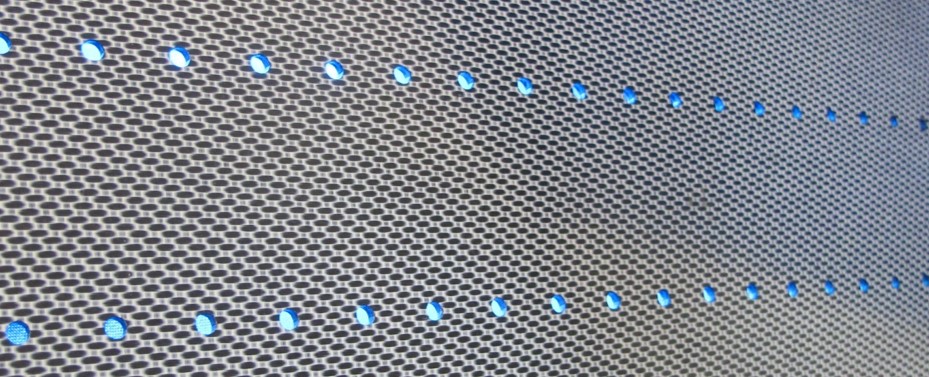
Multispot
Motivation
• Meet the demands of each weld seam geometry
• Adapt the desired intensity distribution within a laser focus
Function / Properties / Characteristics
• Nine individual modularly controllable laser spots
• Partially adapt the laser power to both the weld seam geometry and the material properties
Applications
• Laser transmission welding of unreinforced and reinforced thermoplastics
• Heat conduction welding of carbon fiber reinforced thermoplastics
• Laser joining of thermoplastics to metals
Laser source
• Diodelaser
• Wavelength 980nm
• Max. Power up to 1kW
• 9 individual controllable laser spots
Processed material
• Thermoplasics such as PA6, PE, PP, PPS, PEI
• Carbon fiber reinfroced thermoplastics
• Joining of metal-thermoplastic hybrid parts
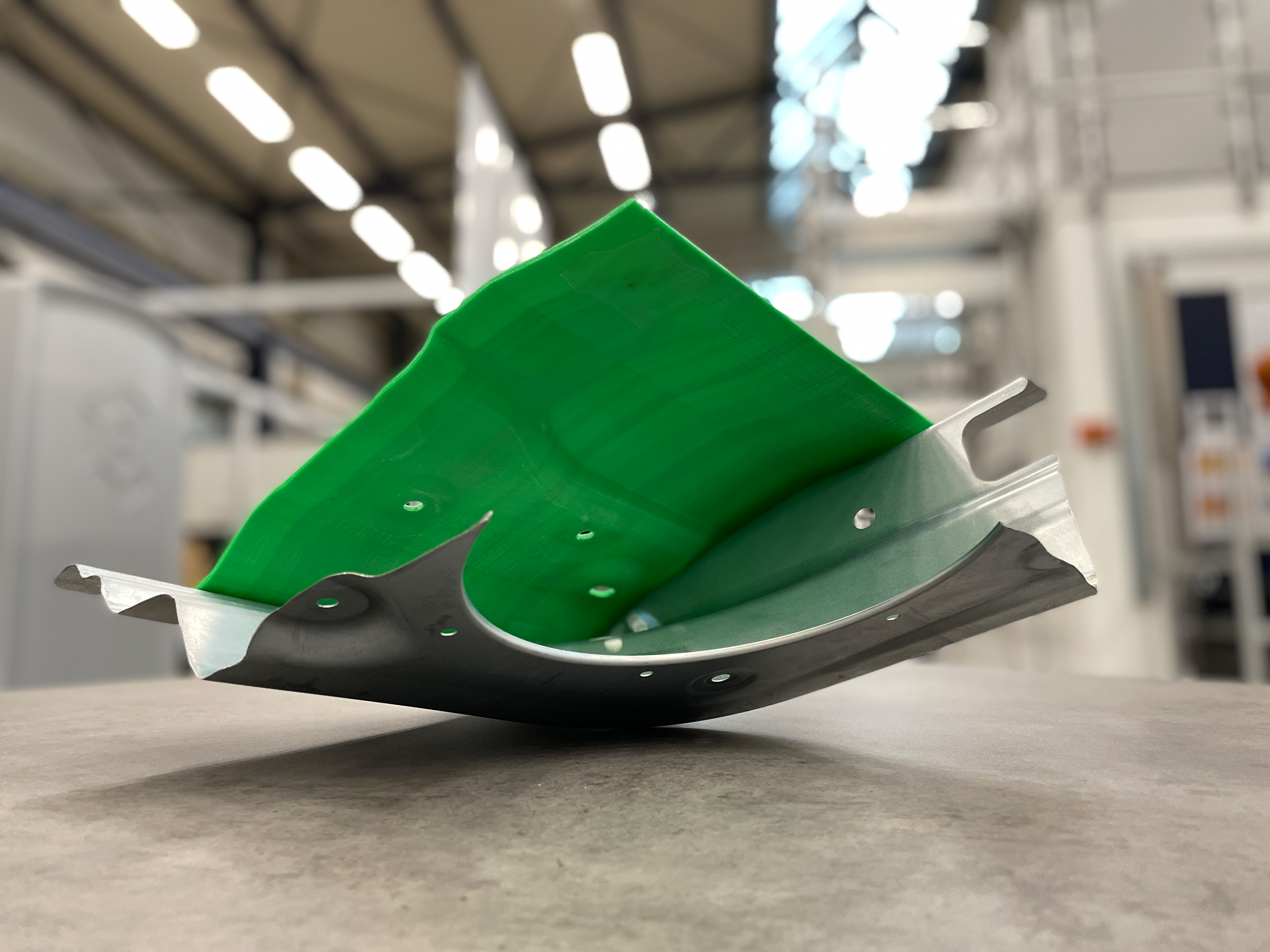
Sol-gel Coating
For the laser annealing of sol-gel layers, the laser beam is guided over the glass sample with the use of a galvanometer scanner or an axis system. In this process, a liner raster is traced to create a homogeneous heat front and shifted over the substrate. The local heating by the laser radiation leads to densification of the sol-gel layer and enables selective densification of areas and shapes of different sizes as well as lettering. After each laser densification performed, the demonstrated sample was recoated and laser-treated again until three fully annealed layers were produced.
Motivation
• Sol-gel coatings are commercially annealed by using a furnace
• For a profitable process, the furnace needs a high capacity utilization rate
• More energy-efficient annealing by the use of laser radiation
• Processing of various sol-gel materials is possible
Function / Properties / Characteristics
• Achieve equal or higher refractive indices with the laser compared to furnace annealing
• Homogeneous layer formation
Applications
• Color effect glasses
• Optical filters
• Improvement of the corrosion and wear resistance (depending on the material: zirconium
dioxide)
Parameters
• Scanning speed: 2000 mm/s for layer one and two
3000 mm/s for layer three
• Focus diameter: approx. 830 µm
• Laser power: 60 W
Laser sources
• CO2-Laser: 10.6 µm
Processed material
• Borosilicat glass
• Three layers of titanium dioxide
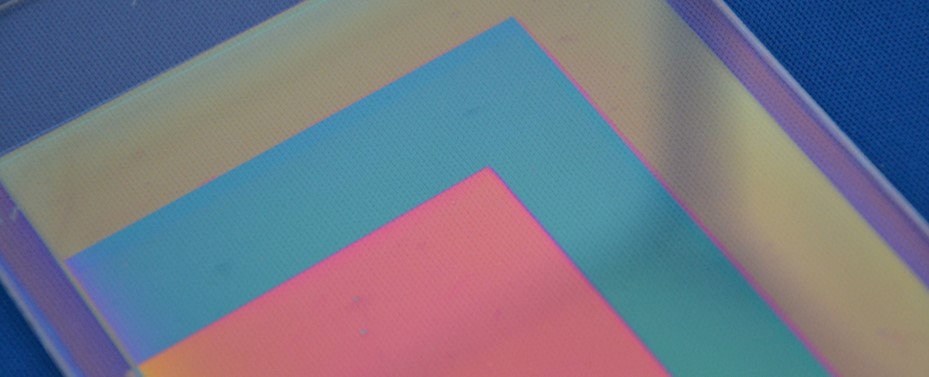
Receive the link to this site per mail
Would you like to access this information again later? Please submit your email-adress here. You will receive a one time mail with the link to the information on our exhibits at the LASER - World of PHOTONICS. If you would like to stay up-to-date to news from the LZH, you find the opportunity to subscribe to our newsletter or our social media channels in the mail.