LASER - World of PHOTONICS: Additive Manufacturing
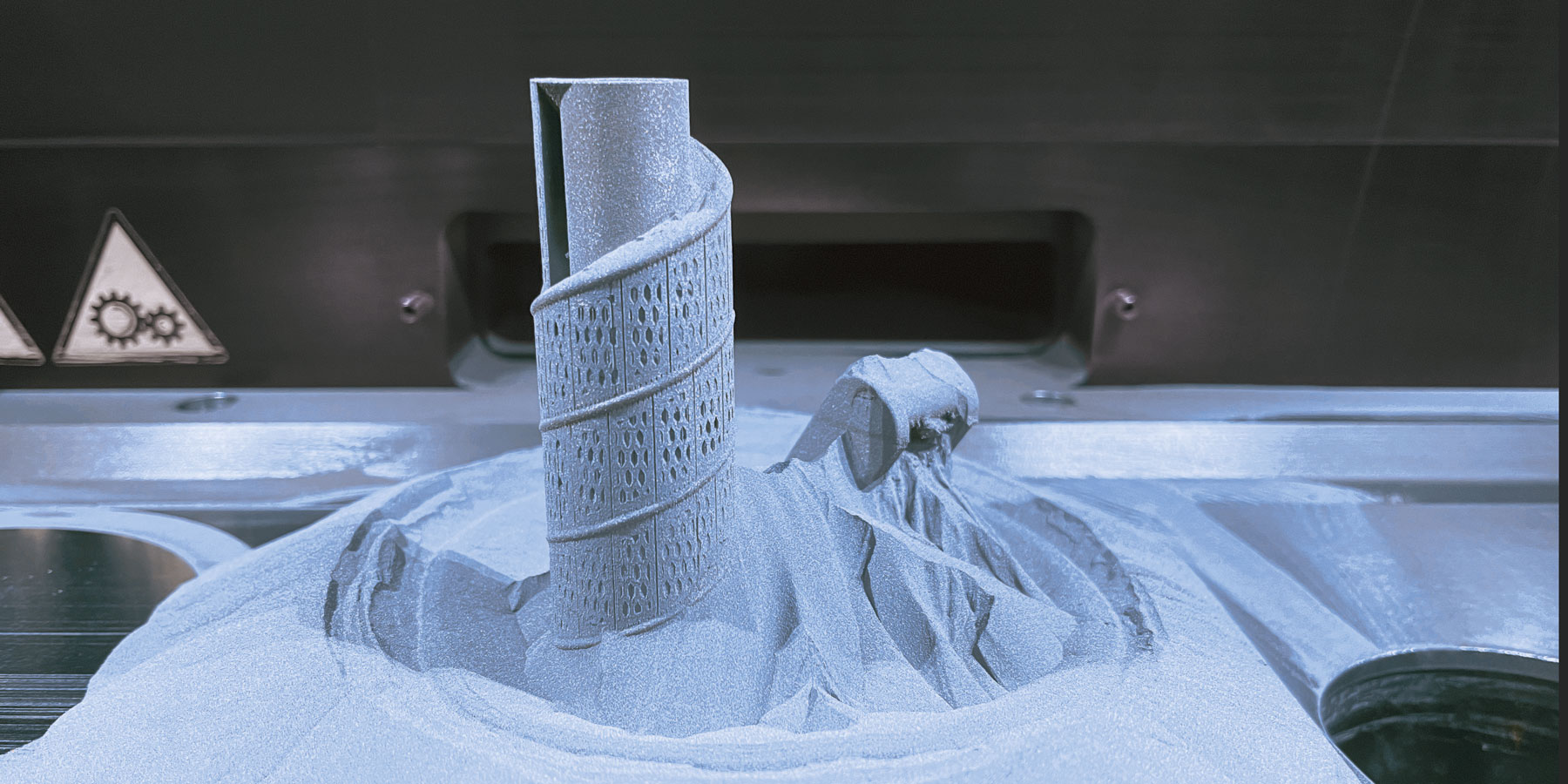
Contact
Phone: +49 511 2788-238
Email: messe@lzh.de
Titanium
Advantages of Titanium
• Light, strong construction metal
• Biocompatible
• Stable process
Applications
• Implants
• Lightweight structural material
• Complex functional integrated parts
Drawbacks of Titanium
• Low heat transfer rate
• Reactive material: Strong oxidative tendency
• Necessity for specialized machines
Oxygen-free production of titanium
• Commissioning of novel PBF-LB system
• Fabrication of titanium in XHV-equivalent atmosphere through silane admixture
Targeted introduction of porosity
• Tailored titanium alloys to reduce oxidation
Recycling of powder material
• Reusing of excess powder
• Reusing of atomized chips from subtractive manufacturing
Parameters
• PBF-LB system: DMG Mori Lasertec 12
• Material: Ti-6Al-4V
• Laser power: 180 W
• Scanning speed: 1000 mm/s
• Hatch distance: 80 µm
• Layer height: 30 µm
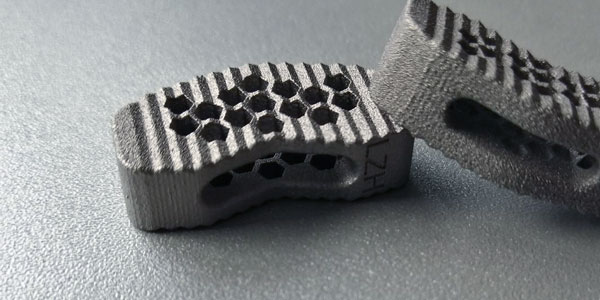
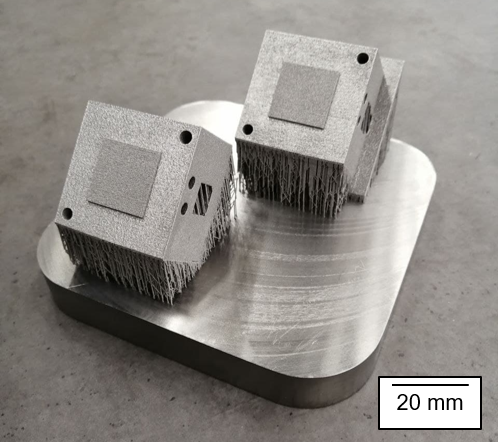
Fabrication of Magnesium WE43
Advantages of magnesium
• Lightest construction metal
• Highly biocompatible
• Biodegradable
Applications:
• Implants
• Lightweight structural material
Drawbacks of Magnesium
• Unstable processing behaviour
• Reactive material: strong oxidative tendency
• Necessity für specialized machines
Stabilizing the melting process
• Hydrogen in inert gas for maximizing remaining oxygen in process
• Improving the air circulation for less interference of processing gases with laser beam
• Different laser source to optimize energy transfer in powder bed
• Higher build plate pre-heating for in-process stress reduction
Processing of novel magnesium alloys
• Tailored magnesium alloys to reduce oxidation (WE43, MgSrY and ZX00)
Increase in economy of the additive magnesium fabrication
• Improvement in build up rate by 230% (increased layer height by 100 %, 20 µm)
Process monitoring of spectral emissions
• Digital twin of fabricated parts --> prediction of material properties
Parameters of current WE43 Demonstrators
• PBF-LB system: SLM Solutions SLM125HL
• Material: WE43
• Laser power: 100 W
• Scanning speed: 400 mm/s
• Hatch distance: 60 µm
• Layer height: 40 µm
→ 100 % relative density
→ sub 150 µm structure width
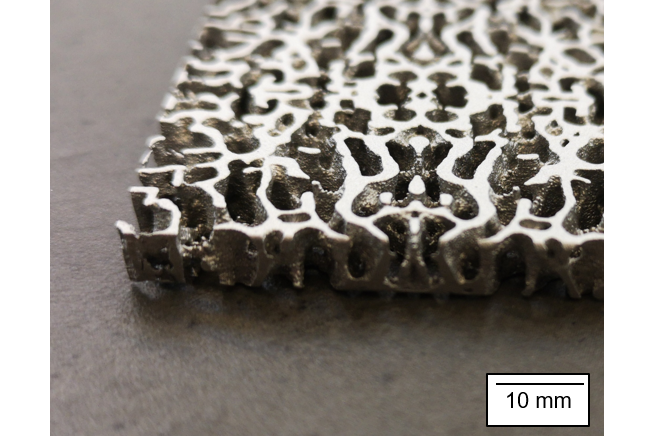
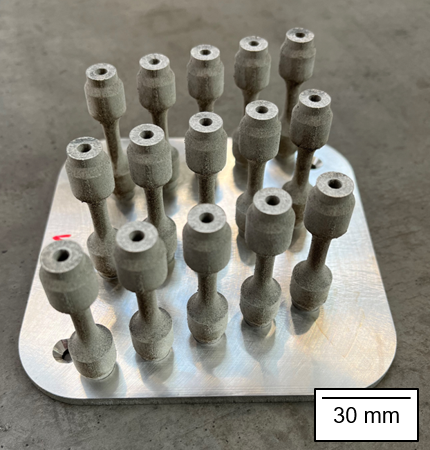
Glass
The Laser Zentrum Hannover has developed a CO2 laser-based process for Additive Manufacturing of glass fibers. For example the implemented fused silica glass fiber is softened by the laser radiation and deposited on a glass substrate in free form by a four-axis system. The conical structure of the sandglass was realized by continuously changing the inner diameter within the printing process. As a result, the layers were applied with a certain overhang to each other, showing the stability of the process in over 60 layers. The flexibility of the process allows the manufacturing of complex 3D structures made of glass with new mechanical and optical functionalities. The components are characterized by high optical transparency and surface quality without noticeable waviness due to the layer structure. Possible areas of application are chemical and medical apparatus engineering as well as optics and structural engineering.
Motivation
• Laser based additive manufacturing of complex glass components
• 3D freeform design for glass components
• New optical and mechanical functionality
• High degree of automation in contrast to conventional glass manufacturing
Function / Properties / Characteristics
• Pure fused silica glass fibers as 3D-Printing filament without binder materials
• Optically transparent components
Applications
• Architecture and facade construction
• Glass apparatus engineering
• Optical systems and optical manufacturing
• Medical Engineering
Parameters
• Laser Power = 100 W
• Feeding rate = 270 mm/min
• Temperature > 2300°C
Laser sources
• CO2 laser
• Wavelength = 10.6 µm
Processed material
• Fused silica glass
• Borosilicate glass also possible
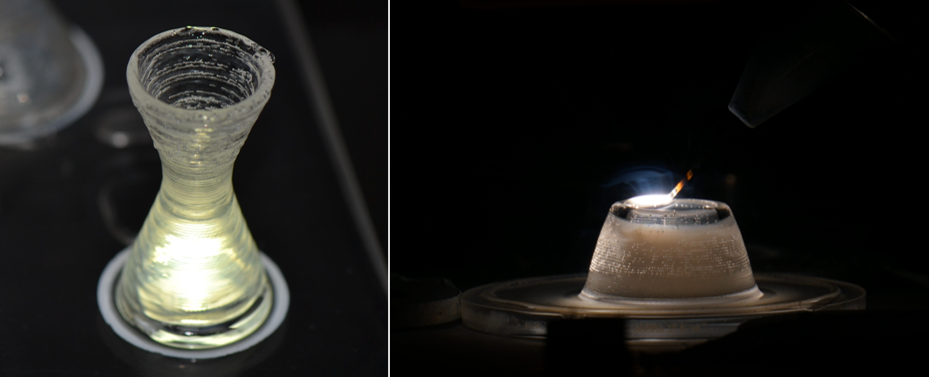
Biocomposites
• Process development for FDM printing of continuous fiber reinforced biopolymers
• Development of a suitable print head for printing continuous fiber reinforced filaments
• Development of a cutting mechanism in the print head to separate the continuous fiber filaments
• Production of facade elements for exterior and interior applications
• Production of segments for the construction of a pavilion as a demonstrator
Motivation
• Exploiting FDM 3D printing with sustainable materials from renewable resources for large-scale architectural components
• Design and fabrication of 3D printed components from biocomposites / filaments with continuous and short natural fibers
Goal
• Development of FDM 3D printing with sustainable materials from renewable resources for large-format architectural components
• Process development for FDM printing of continuous fiber strengthened biopolymers
• Development of a suitable print head for printing continuous fiber reinforced filaments
• Development of a cutting mechanism in the print head to separate the continuous fiber filaments
• Production of facade elements for exterior and interior applications
Applications
• Architectural components
• Production of facade elements in the exterior and interior
• Production of segments for the construction of a pavilion
Parameters
• Dimensions: 200 x 200 x 45 mm3
• Layer height: 0,50 mm
3D-Printer
• ATMAT Saturn FDM-Printer
• Buildvolume: 1200 x 1000 x 1000 mm3
Processed material
• PLA with 40 % wood fiber
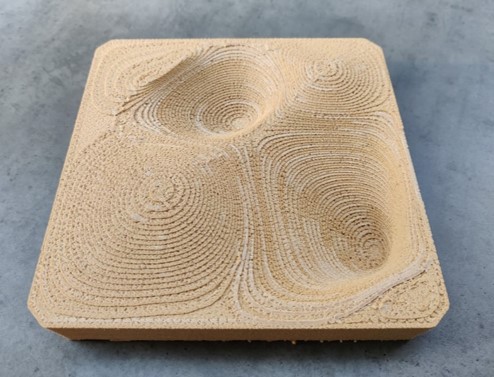
Laser assisted wire arc additive manufacturing
• 3D-printing of large-scale components
• Application: ship transmission housing
Welding power source (EWM Titan XQ R 400 PULS)
• Process: ColdArc
• Welding current: 149 A
• Wire feed rate: 4,3 m/min
• Weldig voltage: 19,0 V
• Shielding gas: 82% Argon 18% CO2
Diode laser (Laserline LDM1500-60)
• 980 ±15 nm; 600 W
• Spot size: 2,9 mm
Function / Properties / Characteristics
• Stick-Out: 15 mm
• Welding speed: 1,2 m/min
• Welding wire: Ø 1,2 mm G3Si1
• Substrate: 30 mm S355JR+N
• Deposited mass: approx. 18,3 kg
• Calculated deposition rate: 2,3 kg/h
• Processing time: approx. 11 h
• Number of layers: 112
• Number of tracks per layer: 16
• Optical elements (Ray path):
dfiber = 600 µm (NA = 0,2)
fcollimation = 63 mm
ffocus = 300 mm
Protective glass
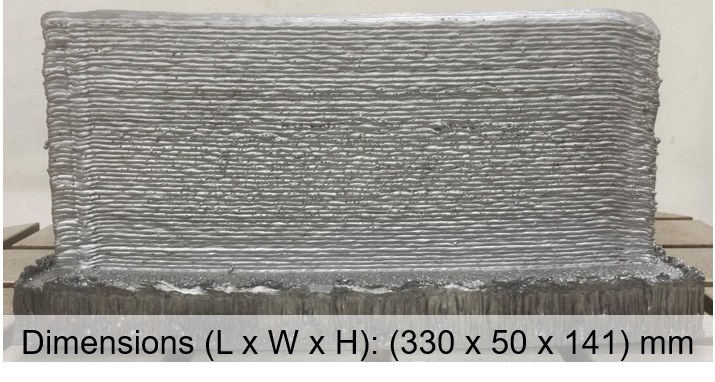
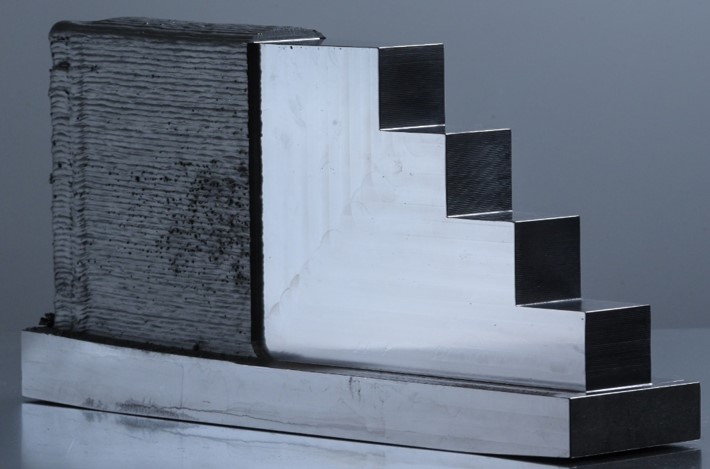
Plant and system technologies: oxygen-free production
Motivation
• Improvement of wettability and component quality
• Minimization of oxygen contamination
• Improved recyclability of the powder
Applications
• Lightweight structures
• Specialized materials
Characteristics
• 10-18 vol% residual oxygen
Parameters
• 30 µm layer thickness
• P = 200 W, v = 1 m/s
• Laser sources: IPG YLR 500 AC (500 W Yb-fiberlaser), 38 µm spot
• Processed material: Ti-6Al-4V Grade 12
• Powder size: 20-53 µm
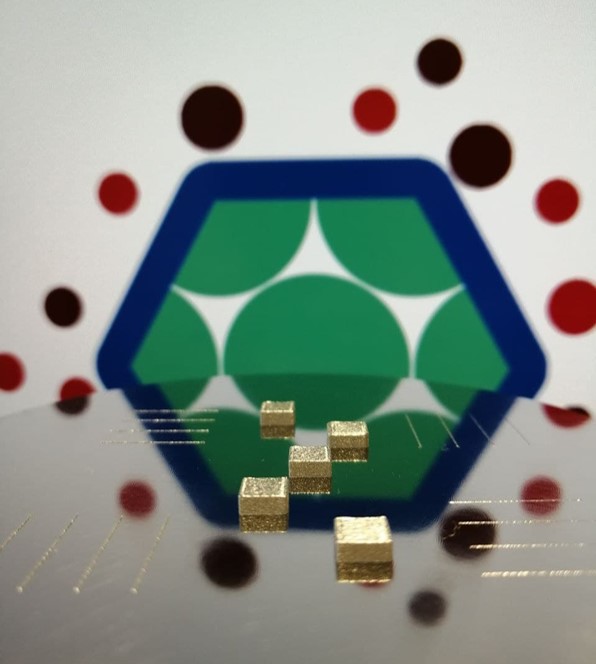
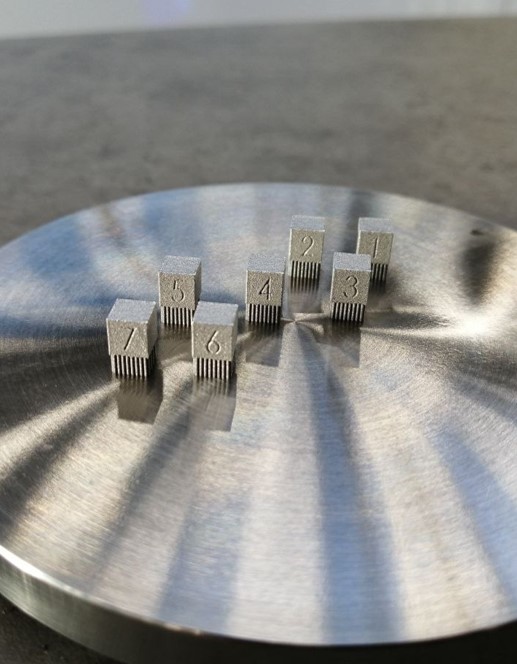
Plant and system technologies: multiple diode coaxial laser processing head
• Up to 6 fiber coupled laser diodes applicable
• Collimation and focusation for each single laser beam
• Individual beams converge at the focal point
• Concept allows the adjustment of the stick-out to the focus position
• Compact and lightweight design with a combined weight of 1.5 kg
• Shielding gas coverage provided within the nozzle holder
• Possibility to provide two wire materials simultaneously to the processing zone
• Investigation of in-situ alloying and fabrication of functional graded materials
• Examination of the mixing behavior
• Directional independence for individual seams is maintained
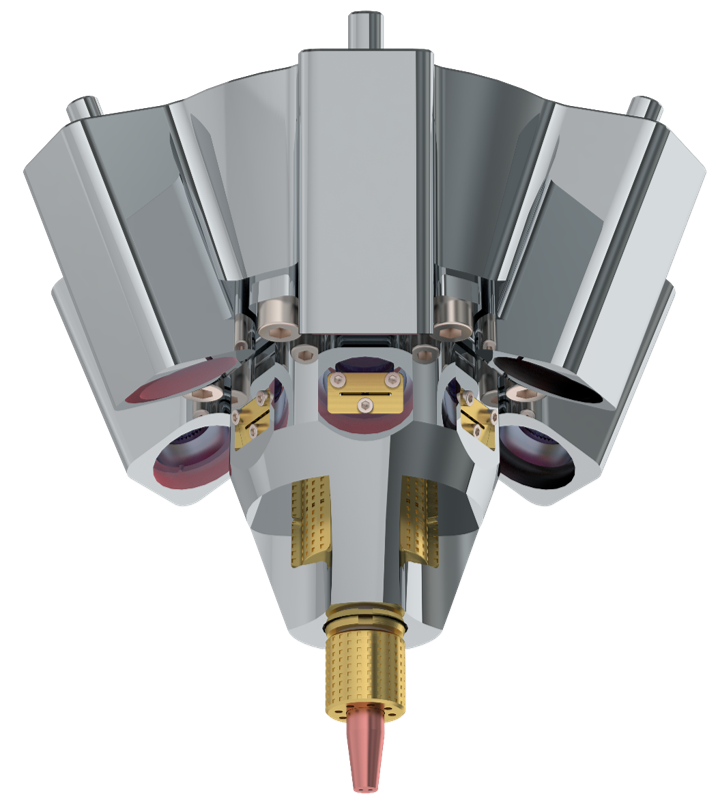
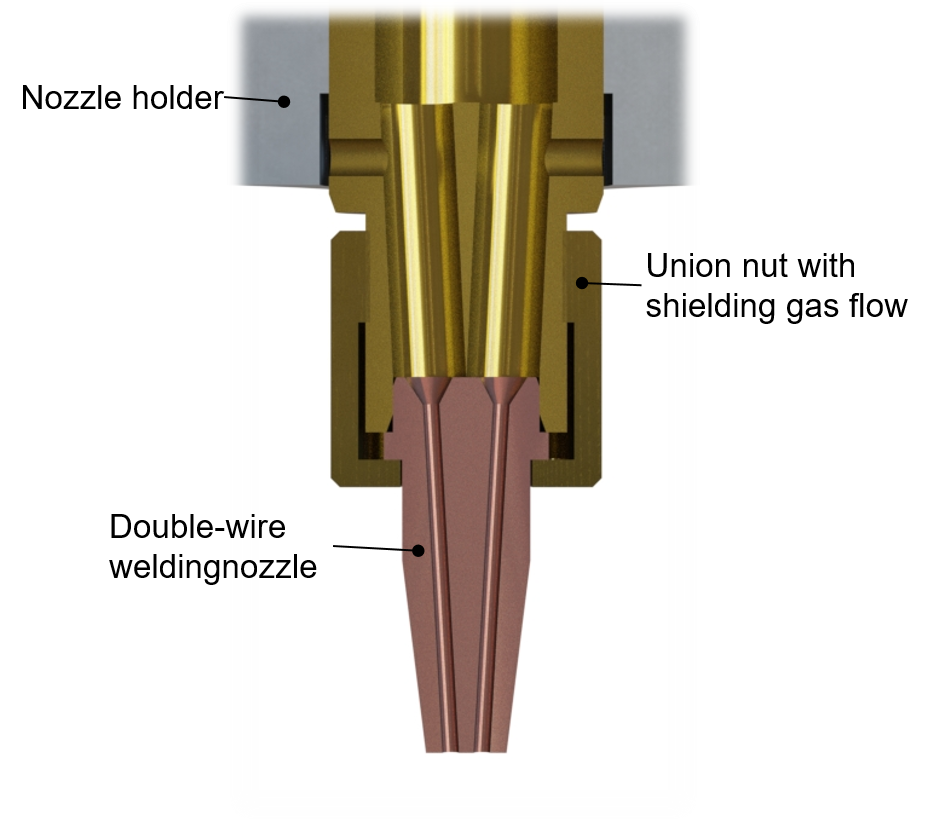
Plant and system technologies: coaxial laser processing head with beam splitter
• Protective glasses and crossjets for optimized protection of the optics
against process emissions
• Focusing lens integrated in the base body
• Integration of a pyrometer possible
• Beam splitter: Four-sided pyramid
• Splitting of the focused laser beam
• Redirection of the partial beams by mirrors
• Individual beams converge at the focal point
• Welding wire is inserted centrically into the focal point
• Concept allows the use of commercially available welding nozzles
• Sealing air to protect the optics
• Shielding gas and other media can be fed to the welding nozzle
Properties
• Weight of the head: 5 kg
• Designed for 4 kW laser power
• Hot and cold wire
• Up to 280 A current
• Low interference geometry and compact design
• Diameter approx. 180 mm and height approx. 250 mm (without collimator)
• Usable wire diameters 0.6 mm to 1.6 mm
• Processable materials: metal materials such as structural, stainless and high-strength steels, titanium
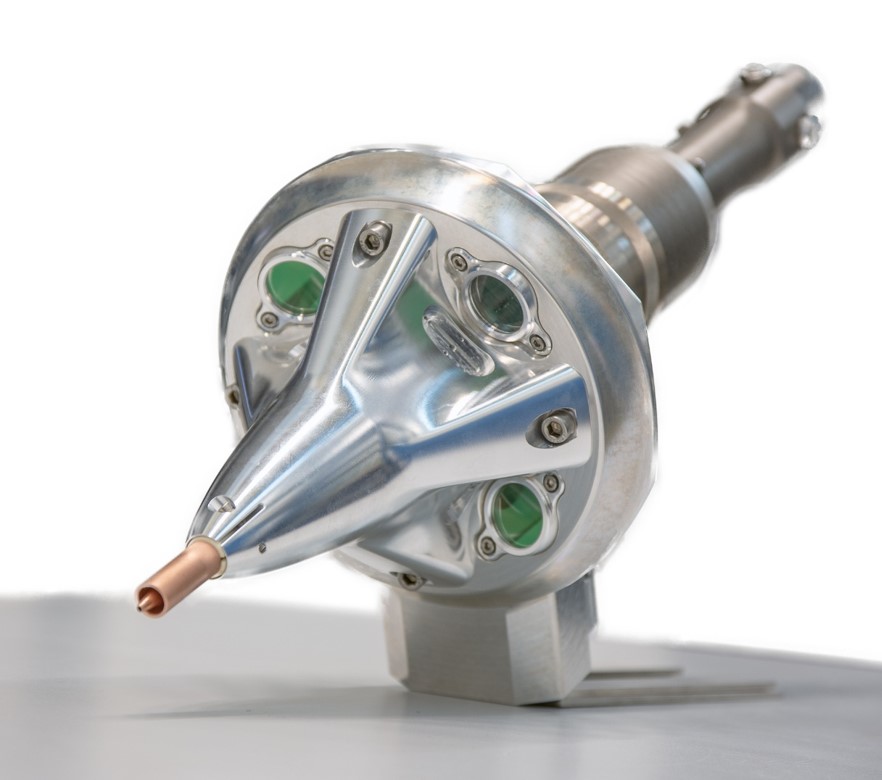
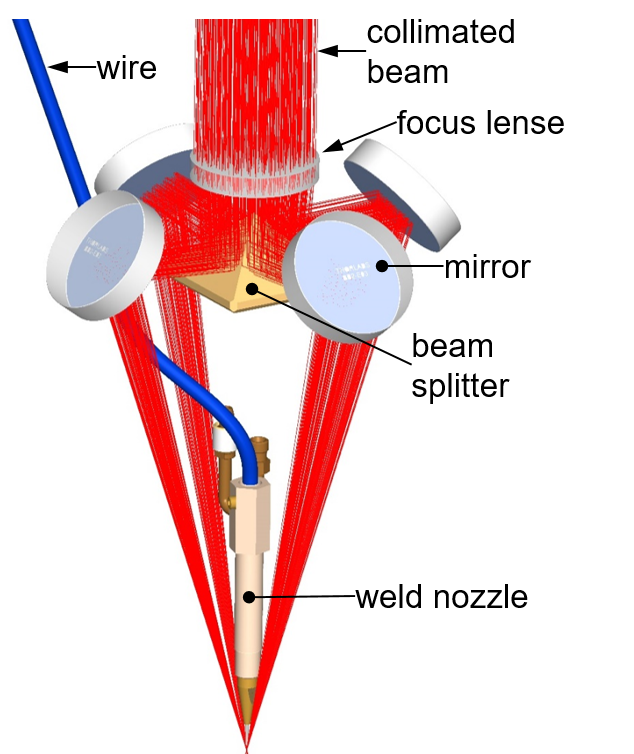
Plant and Systems Technologies: additive & subtractive
Manufacturing of a cutting knife insert
Application: punching of sheet metal components
Properties:
• Substrate material: mild steel
• Coating material 1: chrome-nickel steel (1.4306)
• Good corrosion resistance
• e.g. for cooling channels and aggressive media
• Cladding material 2: chrome-silicon steel (1.4718)
• High surface hardness of approx. 60 HRC
• Wear protection for mechanical loads
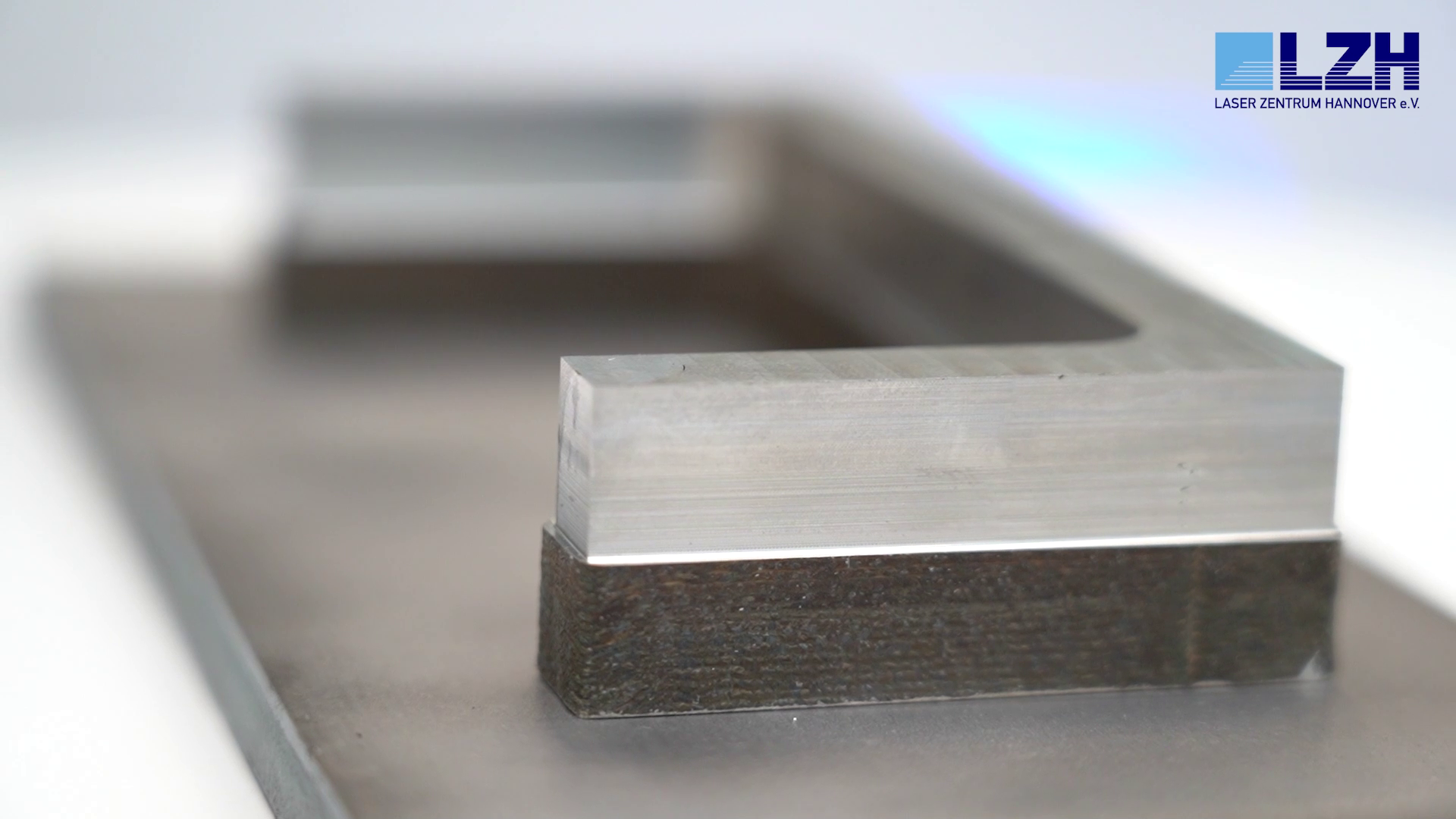
Receive the link to this site per mail
Would you like to access this information again later? Please submit your email-adress here. You will receive a one time mail with the link to the information on our exhibits at the LASER - World of PHOTONICS. If you would like to stay up-to-date to news from the LZH, you find the opportunity to subscribe to our newsletter or our social media channels in the mail.